Installing cellulose insulation using mats
The Filling the Gaps Compensation Scheme Bio-based Materials has started. One of the companies registering to take part in the project is iCell Benelux with its cellulose insulation mat. iCell Director, Wigand Dijkstra, explains the registration.
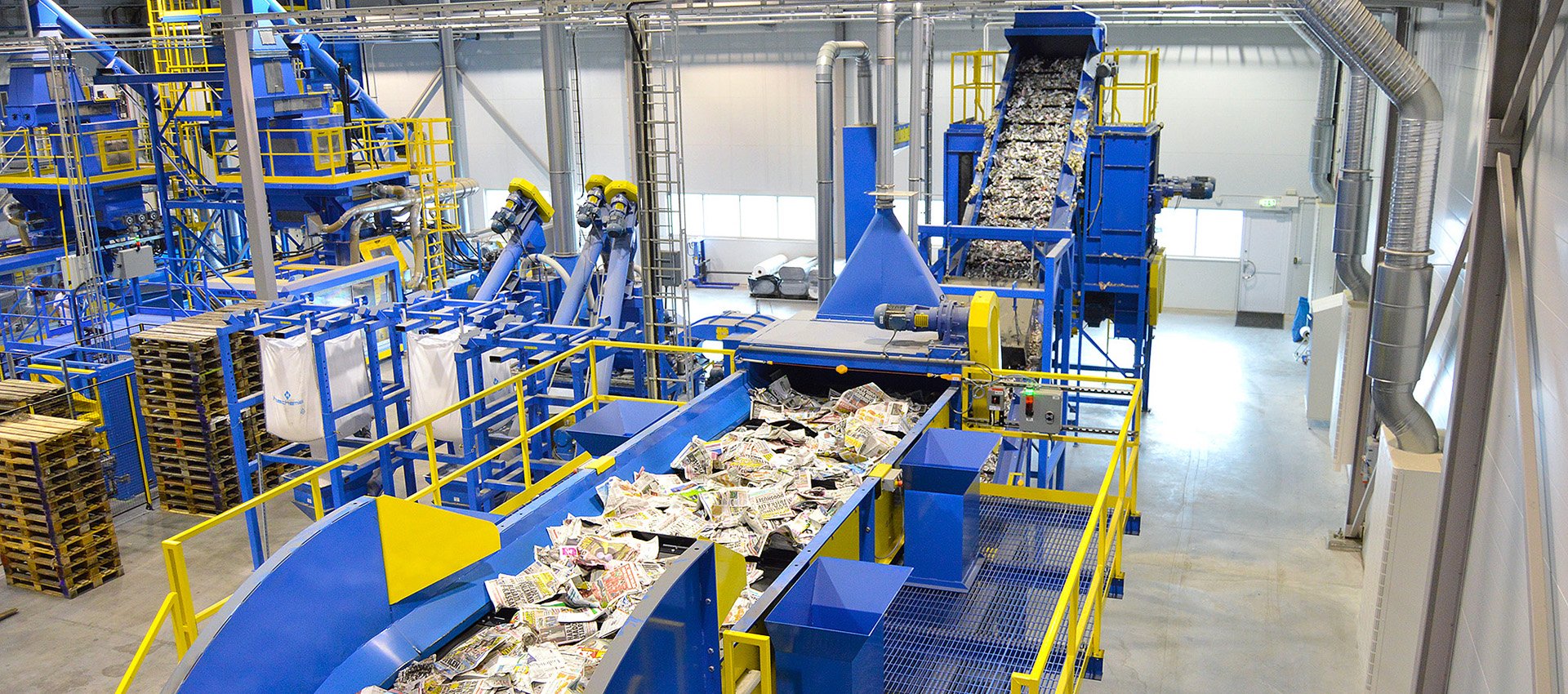
As independent entrepreneur, Wigand Dijkstra started selling LED lighting ten years ago. He did this together with a colleague from his former employer, a producer of plastic pipe systems, Wavin from Hardenberg. This partner put him in contact with a Danish inventor who had developed a process to make insulation mats from fibre-rich material such as flax, seaweed and cellulose. In the end, this process was purchased by Swedish company iCell, a small company that until then only sold loose cellulose flakes. With the insulation mats, the company hoped to innovate the use of cellulose. ‘The mats are made from flakes’, stated Wigand. ‘In many construction situations, it is easier and less cumbersome to use mats than to blow in cellulose flakes. It’s possible to insulate a cavity precisely using a mat and you don’t need special machines. This simplifies the process of installing cellulose insulation.’
But that’s not the only plus point of the iCell products. Wigand is convinced that the iCell insulation mats will achieve an extremely good environmental score in the Witte Vlekken Project LCA survey. ‘We produce the insulation material entirely from a waste product. The basic raw material is old paper and newspapers, which means the mats have a bio-based base and are an ideal cyclical product. The entire production process is also environmentally friendly. Wind and hydro power are used to manufacture the flakes, and there is no soil, water or air contamination. LNG [liquefied natural gas; ed] is also used for the production of the mats. We aim to use residual heat from the construction of a factory in the Netherlands for this. The production process produces no waste as all chippings are reused in the process. After disassembly of the structure in which the mats were used, the material can be reused or recycled.’

We needed to create confidence in the product. Wigand invested half his savings in the Swedish company. ‘The company needed money to develop the mat production process. My wife and I had visited the company in Sweden twice and felt confident in making this investment. It was in any event a conscious choice for us to invest in sustainability. That’s why I’d already been involved in LED lighting. But I could see that I would become one of many in that industry, whereas with iCell’s insulation mats we can offer something special.’
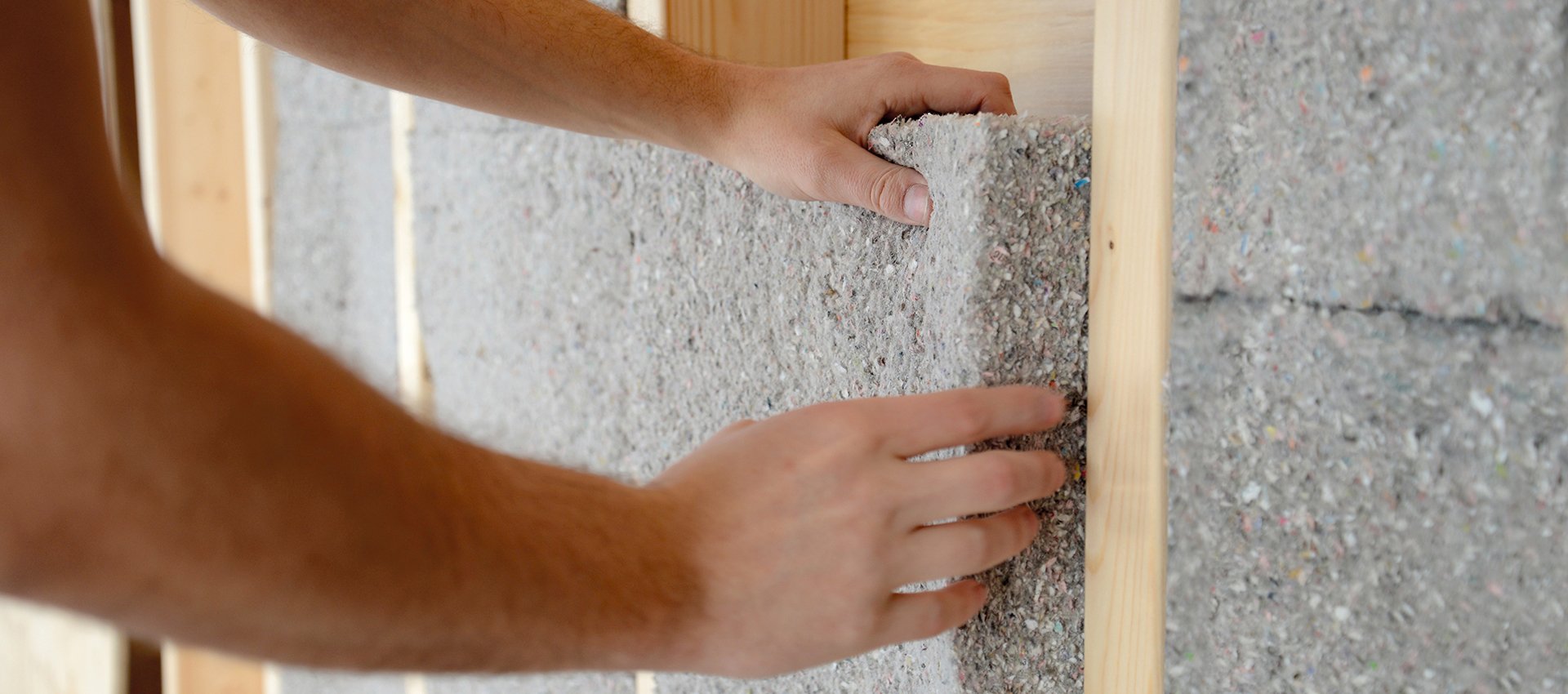
It’s not all easy. Wigan has been introducing the iCell mats onto the Dutch market for some six years now. ‘To be honest, I got into this without much prior construction knowledge. If I’d known how difficult it is to launch a new product as a small enterprise, I’d maybe have reconsidered it. It’s all taken much longer than expected. The construction industry is extremely traditional and you have to pull out all the stops for sales, while there are also a lot of demands on the product in terms of standards and certification. It’s been a bumpy journey.’
However, things are picking up now. Until recently, iCell mats were only available from ecological building material retailers, but the product is now also offered by larger distributors. There’s also a lot of focus on healthy and sustainable construction. ‘Timber construction is clearly on the up. The material’s moisture-permeable structure makes cellulose insulation extremely suitable for roofs, wooden facade elements and timber frame construction. But it’s not only in construction that the product is taking off. Industry has now also discovered us. That’s mainly due to the extremely good acoustic properties of cellulose. Cellulose fibres are better able to absorb vibrations than traditional fibre mats, which results in good sound insulation. One manufacturer of air treatment units is now one of our biggest customers.’
Together with his Swedish partners, Wigand has taken the first steps to develop an LCA for the iCell product. Ultimately, the aim is to include the product in the NMD as a category 1 product. The Witte Vlekken Project is a stepping stone to help market the product better. ‘With twenty-five employees, we’re a small company and it’s not easy to launch your product on the market. We don’t have as big a sales force as traditional insulation manufacturers, while we need to be just as good at demonstrating our environmental impact, heat, moisture, fire resistance and sound insulation performance.’ That’s why Wigand welcomes the Witte Vlekken Project support. ‘This support is not only welcome but necessary if Stichting NMD truly cares about the development of circular and bio-based construction.’
More information on the cellulose mats
Registering for the Witte Vlekken Project does not offer any assurances for the compensation scheme. An assessment will first take place and the scheme funds are limited.
More information on the Filling the Gaps Compensation Scheme
This page has been translated using DeepL
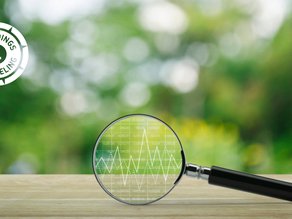
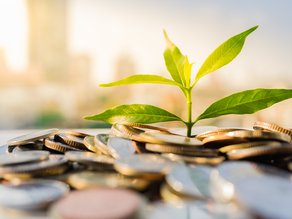
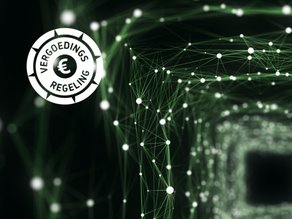
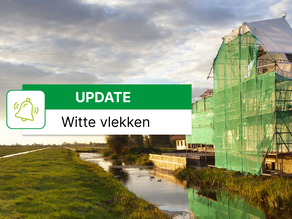