How do you build a sustainable and circular bridge?
Lessons from Bruggencampus
Some four unique bridges can be viewed and used from 14 April 2022 on the site of De Floriade, the huge world horticultural exhibition. Together, these bridges form Bruggencampus; a practical learning environment for developing sustainable and circular bridges.
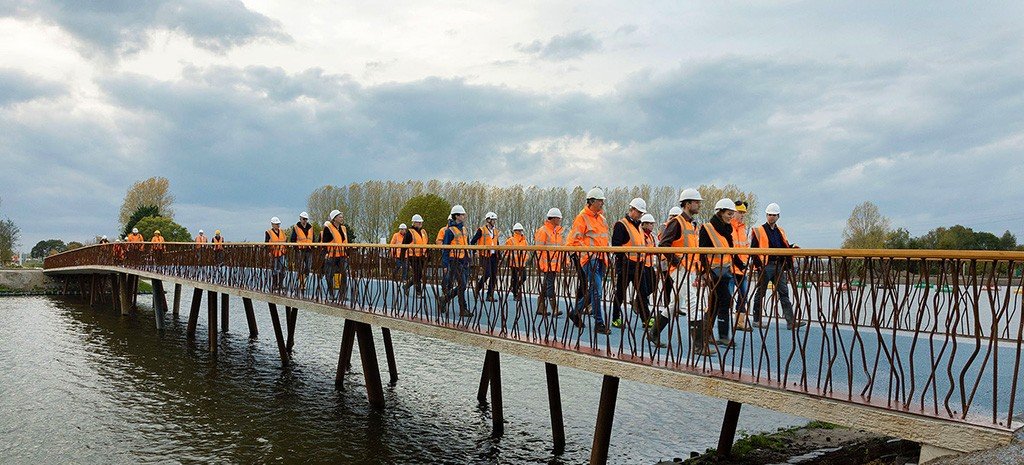
Bruggencampus was established by the Municipality of Almere and the Province of Flevoland and aims to help the Netherlands fulfil its huge national challenge of replacing 85,000 bridges in a sustainable and circular way.
Bruggencampus is the story about bridges made using cement-free concrete, a reused bridge and a bridge with a bio-based bridge deck. These bridges were not only developed on the drawing boards, but were also implemented in practice. Bruggencampus aims to use the knowledge and practical experience gained during the construction of these innovative bridges in the major challenge to replace Dutch bridges. A large proportion of current Dutch bridges was built between the 1950s and the 1970s. Some 40,000 bridges and viaducts now require replacement or renovation. The Bruggencampus learning environment didn’t restrict itself to choosing the materials for the bridges.
Bruggencampus is also involved in the design and implementation aspects of the structures and with the entire development process to ensure a sustainable and circular product. Sustainability Coordinator Guido Meertens from Reimert Bouw & Infra geeft een beschrijving van de twee bruggen van cementloos beton (geopolymeerbeton) die Reimert Bouw & Infra together with Theo Pouw B.V. and Cirwinn realised this, while Sabrine Strijbos from the Municipality of Almere outlines how the innovative tender process contributed to the development of these bridges.
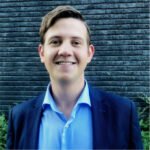
Bruggencampus Flevoland-Floriade is a practical environment for the development and application of innovative and circular bridges. Four bridges were realised during the Bruggencampus programme:
- Beverbrug, a traffic bridge made from geopolymer concrete for the heaviest traffic category. Nicknamed De Spons (sponge) because of the plant containers and tanks that collect and retain rainwater on the bridge for as long as possible, the bridge was developed and implemented by Reimert Bouw & Infra, based on the tender
- Rondje-Weerwaterbrug, a cycle/footbridge made from geopolymer concrete with a high percentage of rubble granulate. Nicknamed ‘Puin’ (rubble), this was developed and implemented by Reimert Bouw & Infra based on the tender
- Tweede Leven bridge, a former pedestrian bridge over the A27 topped with materials from other bridges and railway tracks from Zoetermeer, realised by Dura Vermeer
- Smart Circular bridge, a bridge with a bio-based, fibreglass deck, design by TU Eindhoven.
Sabrine Strijbos: ‘Together with Tjibbe Winkler, Bruggencampus Programme Manager and Joost Bergers, Project Manager at the Province, in 2018 we set about trying to interest market parties in the realisation of two innovative and circular bridges at the Floriade. We started by organising a hackathon. We invited some eighty experts to brainstorm together about building sustainable bridges. There were architects, contractors and structural advisors, as well as several people from entirely different sectors, including the car industry. We hoped to gain entirely new perspectives. The hackathon produced no fewer than 120 innovative ideas and paved the way for us to invite several contractors for a design sprint. We also asked various sustainability and circularity experts to take part. The contractors and experts cooperated on bridge concepts during the kick-off.
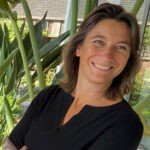
At the end of the meeting, the contractors indicated with which experts they wanted to proceed in the tender process. The experts also did the same with respect to the contractors. Five experts were linked to each contractor in this way. This link was a condition of the tender. We also incorporated sustainability and circularity award criteria in the tender. Ultimately Reimert Bouw & Infra won the tender for both bridges. Dura Vermeer then offered to place a reused bridge at Bruggencampus, while TU Eindhoven submitted a design for a bio-based bridge. That’s how we arrived at the four innovative bridges that have now been realised at the Floriade.’
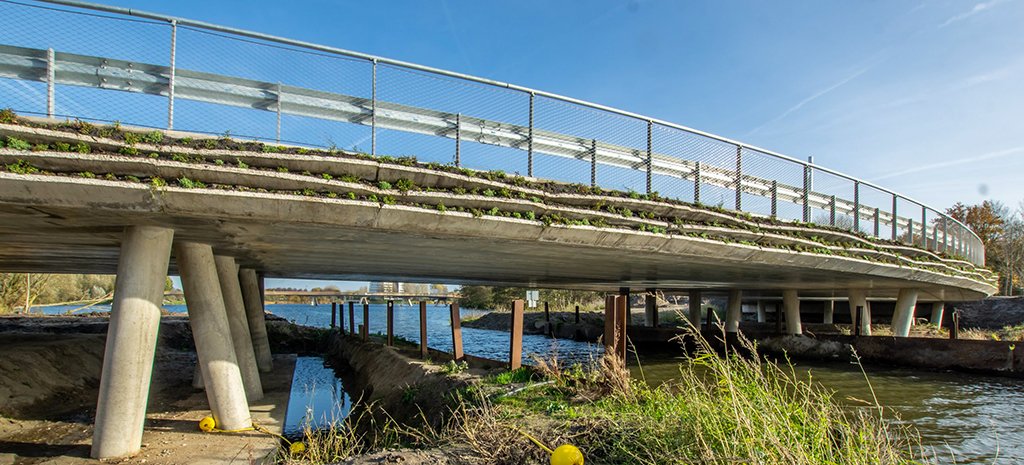
How did the contractors experience the mandatory links with experts?
Sabrine: ‘They didn’t like it initially and asked whether it was really necessary. ‘I don’t need other people because I have my own team’, they stated. But they gradually saw that this added value. The addition of the experts linked to a contractor resulted in innovations that would not otherwise have been realised. A concrete example of this is the Beverbrug that used tanks to collect rainwater from the bridge deck and retain it for as long as possible.
Was the Municipality of Almere satisfied with the innovative approach to the tender?
Sabrine: ‘Initially, we struggled with how specified the tender needed to be. If specifications are too detailed, you stifle innovation and creativity, while if you leave the description too open the contractor doesn’t really know what is intended. We discussed this with the contractors, which led to us clarifying the award criteria description.’
Essentially, geopolymer concrete is comprised of the same raw materials as traditional concrete, namely a cement-based material, aggregate (sand and gravel), water and any admixtures and fillers. The cement-based material in geopolymer concrete comprises alkaline-activated raw materials (known as precursors). This includes well-known residues often already used in cement, such as blast furnace slag and fly ash, but could also include potential applications such as soil clays, river sludge and residues from waste-to-energy plants. In traditional cement, blast furnace slag and fly ash are activated by calcium hydroxide (product from the reactivity of hydrated Portland clinker), whereas in geopolymer concrete an activator is added to activate the alkaline reaction. As a result, there is no chemical hydration (reaction with water) but polymerisation.
Source Cementonline
How did Reimert Bouw & Infra end up choosing geopolymer bridges?
Guido Meertens: ‘Initially, we made a reference study of various types of bridges. Based on that study, we discounted the composite bridge almost straight away as the environmental costs of this type of bridge proved considerably higher than those of steel and concrete. We then focused on the details of the tender brief: an 80-year lifespan, the lowest possible carbon emissions, maximised reuse of materials, maximised reduction in material use, the highest possible benefits for Floriade and maximised positive spin-off effects.
We used DuboCalc to calculate the environmental costs. The carbon emissions were used as guideline. Following a centre of gravity analysis, we concluded that a concrete bridge deck would have a major impact on environmental costs. In consultation with Utrecht-based Theo Pouw B.V., which had also built a new and sustainable concrete plant on the Cirwinn site in Almere, we then settled on geopolymer concrete. What is special about this project is that we were able to use the geopolymer concrete for the structural parts of both bridges. And everything was based on a KIWA certificate. This means you’ve already made hefty carbon reductions straight away. Compared with traditional concrete, geopolymer concrete delivers carbon reductions of around 65%.
However, it wasn’t only the use of geopolymer concrete that resulted in carbon emission reductions. Focusing on local transport and reusing materials also enabled us to reduce the Beverbrug’s carbon emissions by as much as 38% compared with a design based on traditional building materials.
For both bridges, the approach was to use raw materials released from local residual streams. The Municipality of Almere supplied concrete rubble that we processed into concrete granulate in our crusher. Some 50% of the aggregate for the geopolymer concrete is comprised of recycled Almere concrete. This innovation was nominated for the 2021 Betonprijs. Other materials also fall in the ‘reused’ category. The rebar for the Rondje Weerwater bridge also originated from the Almere residual stream and was used for the bridge rods. The tubular steel piles under the bicycle/footbridge are piles that have been given a second lease of life.
Many different parties are involved in the design and realisation of bridges and viaducts, and all use their own IT systems. This means that we lose a lot of knowledge and information during the partnership. Smarter use of IT should largely prevent failure costs, which is why Bruggencampus started with a state-of-the art Common Data Environment to streamline and optimise communications and processes between client and contractors. 2D drawings with 3D BIM Models at different moments in time are linked to costs, allowing the actual situation to be mixed with the planned situation. This innovation was also embraced by the municipality. The entire park infrastructure is now being mapped in the GDO, which can feed the municipality’s digital-twin with verified and validated project data.
‘What conclusions has the Municipality of Almere drawn so far from Bruggencampus as a learning environment?
Sabrine: ‘In any event we’ll be continuing to develop the GDO. If you want to promote the use of local waste streams, it’s important to know where you can find materials and know what their current status is. This means that we need to take significant steps in digitising our structures.
We’ve learned a lot so far, both in terms of knowledge of materials and the development process. With our colleagues from Urban Space and Area Development we’ll be examining how to apply this knowledge in the municipality and in the province. Some 3,000 bridges in Flevoland are scheduled for renovation or replacement before 2050. If we want to realise our climate and circularity ambitions, we need to do that using a different approach than we’ve used until now. Bruggencampus has laid the foundation for a different approach. We can also apply this approach to structures other than bridges.
We’re also working hard on knowledge sharing. We aim to share the Bruggencampus knowledge with the rest of the Netherlands. The Bruggencampus website contains a lot of information. We programmed six events during the Floriade that are accessible to everyone interested in our innovative and circular approach.’
More information:
This page has been translated using DeepL
Milieudatabase.nl would like to demonstrate projects with a low EPB. If you’re working or have worked on a project with an EPB of 0.5 or lower, please let us know. You can register your project via the following email address communicatie@milieudatabase.nl
Related articles
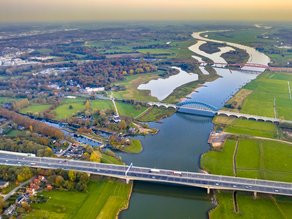
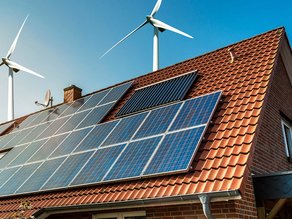
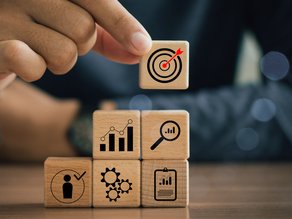
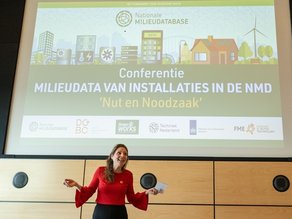
Blijf op de hoogte
Meld je aan voor onze nieuwsbrief en ontvang maandelijks updates over duurzaam bouwen, milieuprestatie, milieudata, beleid en ander relevant nieuws vanuit Stichting NMD.
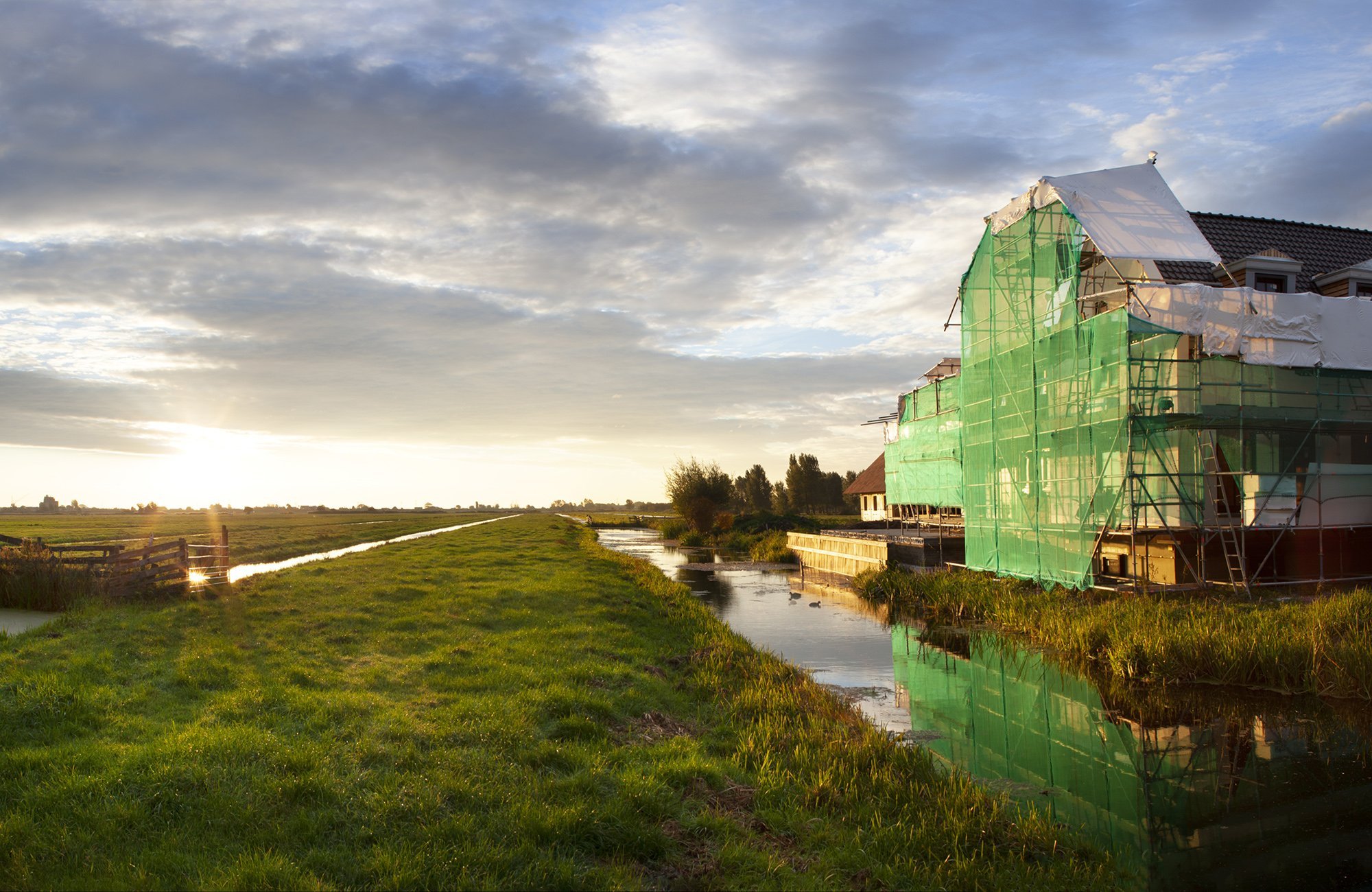