Energiehotel part 2; sustainability as starting point
How do you make a sustainable building? Milieudatabase.nl puts buildings with excellent environmental performance in the spotlight. Milieudatabase.nl had previously written about the Energiehotel along the A12 near Ede that takes its name from the PV panels on its facade. According to calculations these will ensure that the construction work generates more energy than it consumes.
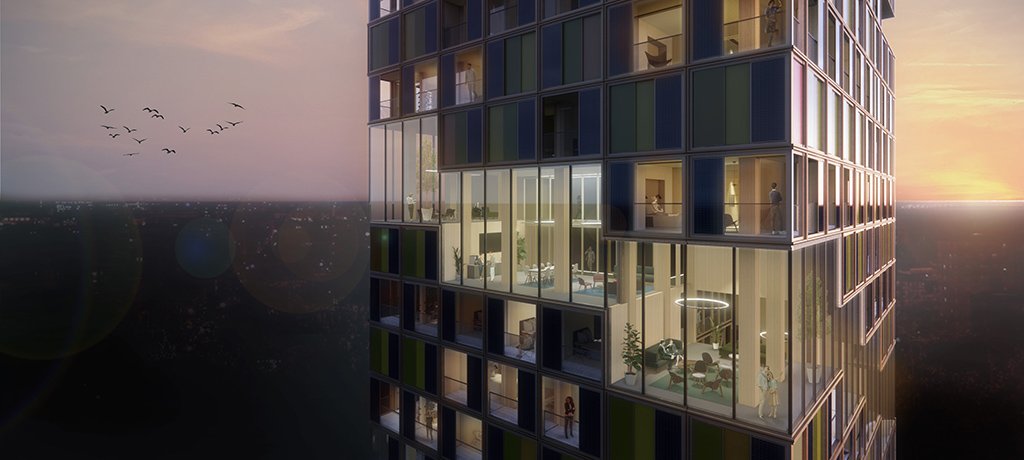
The hotel aimed to open its doors to guests in 2022 with an EPB score of 0.442. The EPB calculation made in the context of the Environmental Investment Allowance (EIA scheme), is not yet final. But it has always been the intention of project developer Gerben Kuipers from the Noorderenggroep to keep the EPB below 0.5. (*) This article takes a closer look at how Energiehotel’s sustainable design came about and which measures are crucial for the low EPB score.
Kitchen table
Discussions at the kitchen table with his children led him to use sustainability as the starting point for the design. ‘My children said “Dad, think carefully before you start”. They’re all involved in sustainability for their work.’ The conversation with Gerben Kuipers revealed how concerned he is with every detail and how he considers everything: ‘You have to involve the cleaner because they know exactly how long a certain floor covering lasts and what the maintenance costs are’ and ‘we had a groundwater pump installed because if you sell a 200 cl cup of coffee you need around 5 litres to flush the toilet’. Now that the design process is in the final phase, the developer has concluded that he can achieve an EPB score of below 0.5 thanks to the choices he made in advance. ‘You can’t add in sustainability at the end as it’s then too late. You have to be thinking of that from the very outset. Everything is interrelated. If you introduce something at the end, you disrupt the cohesion. It’s now become apparent that we could have saved nine piles as the total structure is a lot lighter than we anticipated in advance. But it’s too late to change the plan now so we’ll use that as an improvement point for next time.’
Project features
Use functions: | hotel |
Gross Floor Area: | 8,321 m2 |
Building service life: | 75 years |
Project duration: | 2018 -2022 |
Address | Laan der Verenigde Naties, Ede |
Client: | Noordereng Groep, Bennekom |
Architect: | DP6 architectuurstudio, Delft |
Advisors: | ABT, Delft-Velp; DGMR, The Hague; DWA, Gouda; De Groene Jongens, Utrecht; Hedgehog Company, Amsterdam; Hupperts Architectural Engineering, Breda |
Implementation: | Dura Vermeer, Hengelo; HEKO, Ede; Ferross, Oss |
ECI and EPB = score Energiehotel
calculated using GPR Material version 5, NMD product database, version 3.0, 5 December 2020
ECI | EPB | ||
A | Production phase | 257,999 | 0.413 |
A | Construction phase | 10,100 | 0.016 |
B | Use phase | 75,862 | 0.122 |
C | Disposal phase | 8,865 | 0.014 |
D | Outside building service life | -77,108 | -0.124 |
TOTAL | 275,719 | 0.442 |
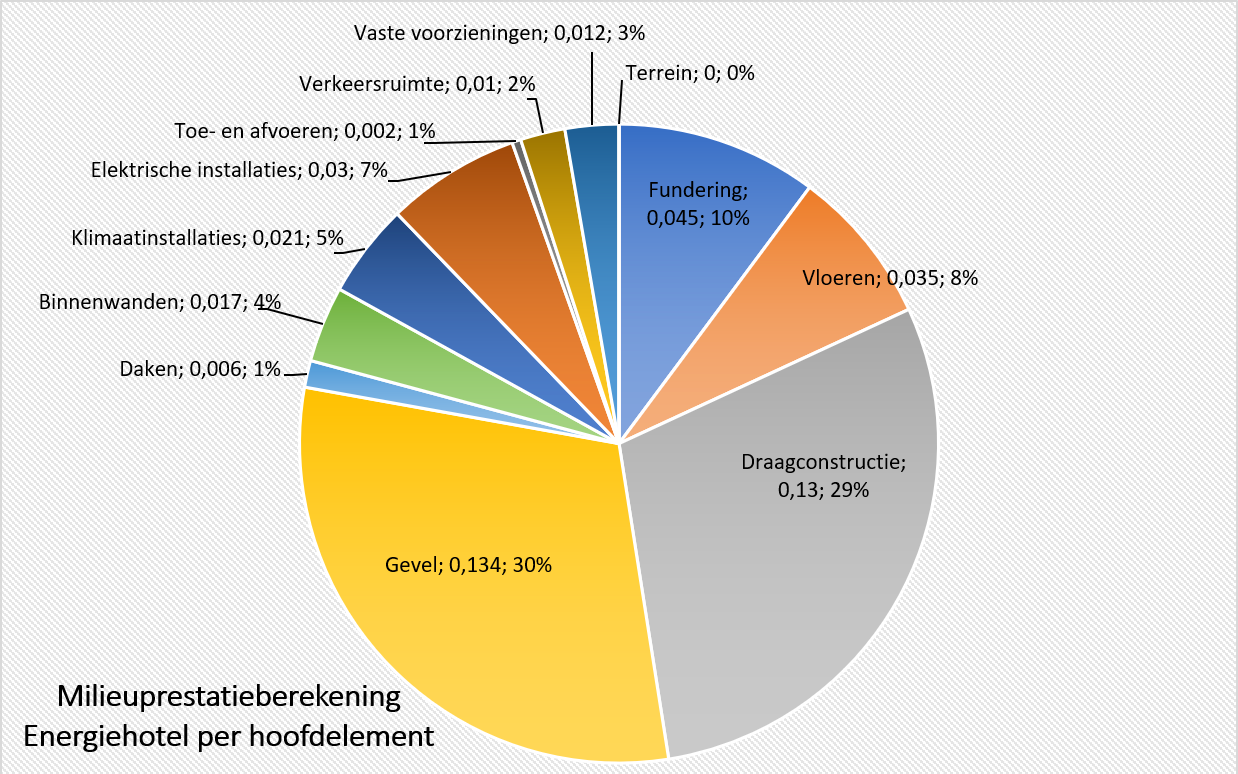
Cross-laminated timber (CLT)
Studying the EPB calculation, it’s the use of cross laminated timber that stands out. 22,000 m2 of CLT was reserved for the supporting structure of floors and walls, while 153,000 kg of laminated European softwood from sustainably managed forests was used for the columns and beams. It should also be noted that the central staircases are produced from European softwood. Concrete is also used but is limited to the foundations and the ground floor plinth. Sustainable concrete product variants were also selected including the VBI fast slab floor Green.
The CLT for the walls and floors above the ground floor plinth was used to produce timber modules that are placed in a steel frame. Under the name ‘Houtkern’, Gerben Kuipers developed the modules together with Heko Spanten from Ede. The prefabricated modules can be linked together, making it possible to create large rooms. ‘Think of them as separate building bricks. We’re using them to make hotel rooms right now, but you can also use them to build homes, schools or offices. You can deliver the modules as a shell but it’s also possible to furnish the rooms with all the required installation components.’
The Houtkern modules, which are made from certified FSC timber, formed the solution for the major issues that Gerben Kuipers was struggling with in advance. He doesn’t like users of his buildings needing to invoke the building guarantee scheme. How do you combine sustainability with good construction quality that’s also affordable? ‘Wood is sustainable. It’s a renewable material and contributes to carbon reduction. We resolved the structural problems involved in timber construction, including noise transmission and the structural limitations of high-rise construction. The steel frame enables us to build to heights of 80 metres. The modules are surrounded by air and therefore have no noise issues.’
EIA/Vamil
In order to benefit from the MIA/Vamil (Arbitrary depreciation of environmental investments scheme), the project’s EPB score must be 0.5 or lower, a web-based materials passport must be available and at least five building materials need to be listed in the National Environmental Database as category 1 declarations. The final condition is mainly intended to promote the project’s circularity. From the five environmental declarations it must be clear that the materials contain at least 50% secondary raw materials by weight, or that they are reusable building materials with at least 20% product reuse in the end-of-life scenario, or a combination of these.
Gerben Kuipers: ‘It’s not yet clear which environmental declaratios we’ll use. We’re considering developing new LCAs. That is a difficult process, which is why we’re doing that together with the Groene Jongens from Utrecht and the Hedgehog Company from Amsterdam. In any event, our focus will be on wood. De Houtkern is a modular system. It means that it can be disassembled and reassembled and that’s an important condition for circularity. The steel and wood can in any event be recycled. But there are also many opportunities for high-quality reuse due to the extent and potential for disassembly.’
Reflecting on the Energiehotel development process, Gerben Kuipers no longer wants to return to the old building methods. According to him, a modular timber construction system offers only advantages. ‘I can deliver much better building quality with prefabricated modules, as that quality is much more manageable in the factory than on a building site. If the modular products can be delivered to the construction site ready-made, I can make do with a much smaller construction site and the entire construction process is faster. Building with timber is light, so I don’t need such heavy duty equipment. Basically, we need to do construction differently. We need to transform the construction process. Industrial construction is the future and the construction site will be an assembly site. And that means that you need to consider your design well in advance, because it’s too late once you’re at the construction site.’
Milieudatabase.nl would like to demonstrate projects with a low EPB. If you’re working or have worked on a project with an EPB of 0.5 or lower, please let us know. You can register your project via the following email address communicatie@milieudatabase.nl
This page has been translated using DeepL
Related articles
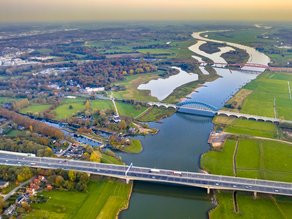
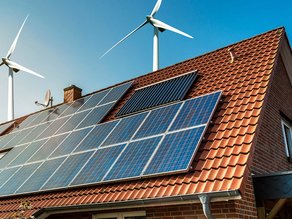
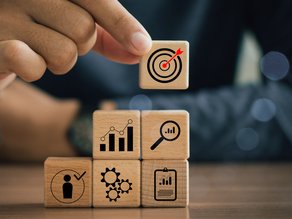
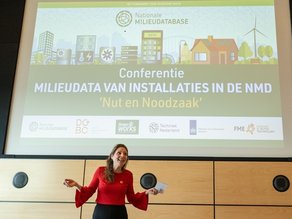
Altijd actueel:
nieuws over duurzaam bouwen en milieuprestatie & milieudata
Ontvang elke maand het laatste nieuws duurzaam bouwen, milieuprestatie,
milieudata, inclusief tips en voorbeelden uit de praktijk.
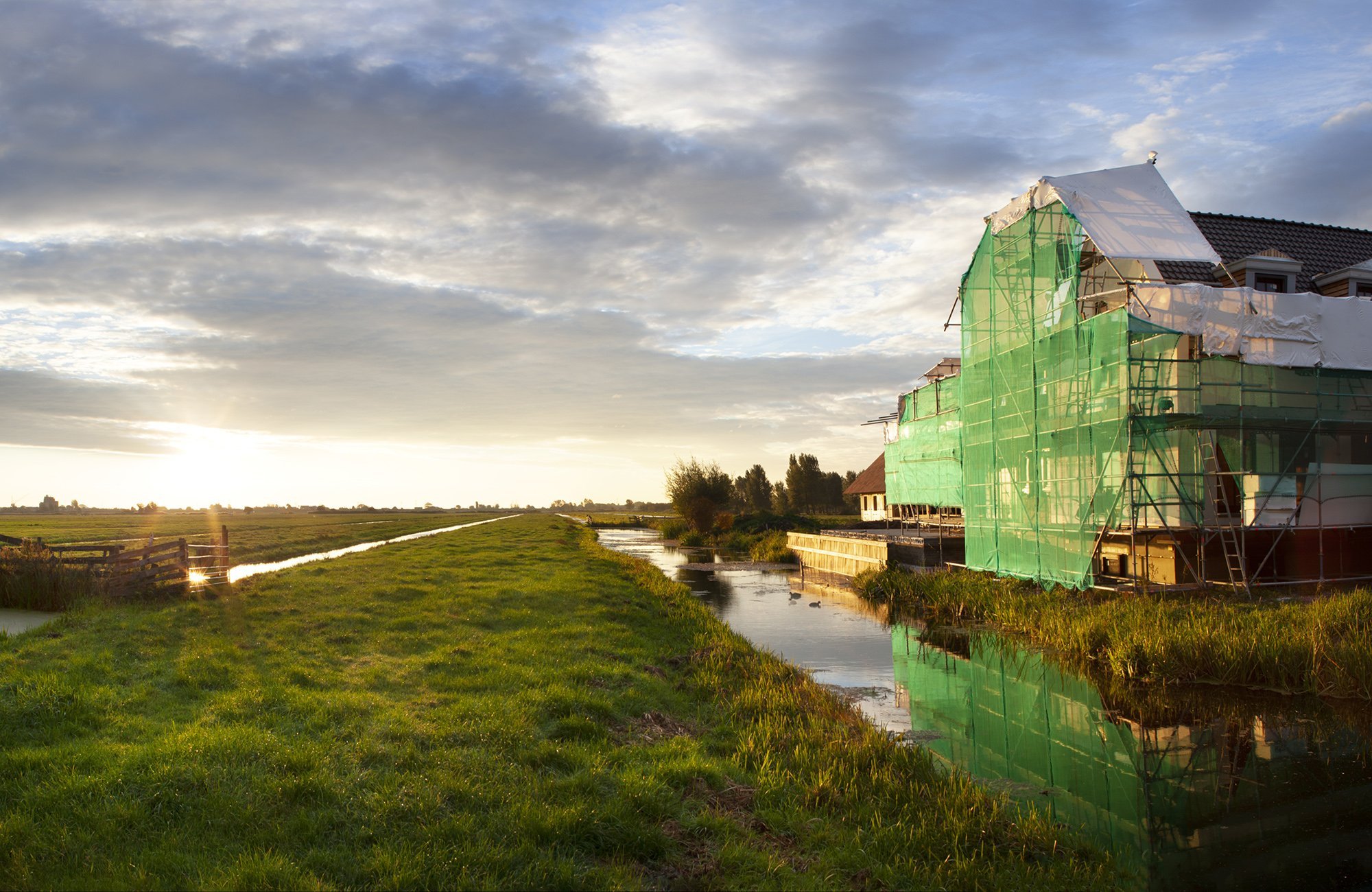