GSF Glasgroep makes recycled insulating glass:‘ Towards an equivalent circular glass factory’
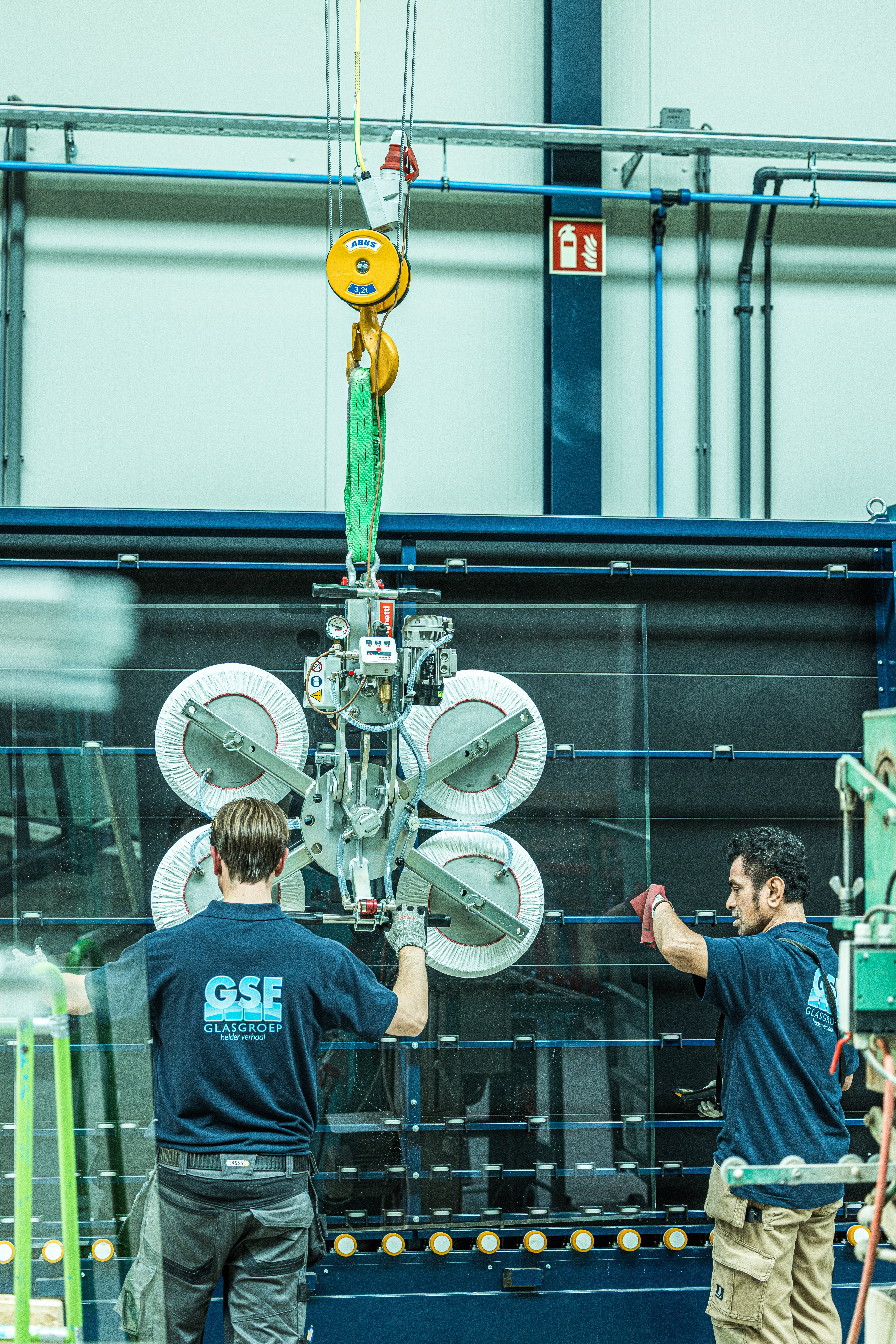
About three years ago, in the middle of the corona crisis, GSF Glasgroep decided to investigate whether insulating glass could be reused in such a way as to retain its high insulation value. The answer turned out to be: yes, it can. Meanwhile, the circular insulation glass isoMAX Circutherm 50 is also listed with category 1 data in the NMD. The MKI turns out to be 72% lower than traditional insulation glass. Director Maarten Rood: ‘Our goal is to develop a circular glass factory equivalent to a traditional glass factory. So that we become comparable to traditional insulating glass in terms of price and volume. We are already moving in that direction."
Maarten started working at his parents' glass company about 15 years ago. A traditional glass company that operated very locally in and around Lelystad. In 2015, he took over the company and became managing director.
‘Gradually, we started working more for government and semi-government organisations. Municipalities, housing associations, insurers, the NS. From that corner in recent years, the question of how we could reduce the CO2 emissions of our material came more and more frequently. Glass is one of the most hefty building materials when you consider the CO2 emissions from the construction or renovation of a house or building. So the question came to us: can't we start reusing it?’
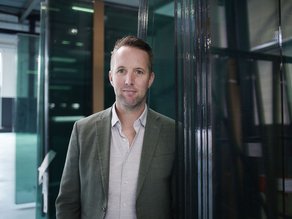
GSF Glasgroep
Maarten Rood
Scientific research
‘We actually always say in the Netherlands that glass is reused. It is. I think in the Netherlands we have perhaps one of the best recycling systems in the world. But what happens with that is that the glass goes back into the furnace and is used for bottles and glass wool, for example. Reusing the panes as a whole, that never happened. The thinking was also that this was not possible for insulating glass. Because an existing window is too contaminated for that.’
‘Now we decided to investigate it anyway. We couldn't do that on our own. We know a lot about glass, know well where to get it and how to apply it. But we know little about strength calculations. And what would reuse do to the insulation value of the glass in the long term?’
A collaboration with the Hogeschool van Amsterdam and TU Delft offered a solution. ‘And the great thing was, due to the corona crisis there was more than enough room in the schedule to do this research. So we supplied glass and the university was then able to conduct research using climate boxes. In a few months, this simulated what the effect would be after 20 years. It thus became clear that you can use existing windows just fine to make insulating glass again.’
Circular production process
The next step: actually going into production. ‘We soon found out that existing manufacturers did not want to pick this up for us. So we decided to set up a production site ourselves.’
GSF Glasgroep has since been collecting used glass itself; harvesting it. ‘We invested in bucks to store and transport the glass safely and in one piece as soon as it comes out of a home or building. So glass that is not broken, but needs to be replaced because it no longer meets its insulation value, is no longer thrown in the container, but goes to our production site. There, we have a large machine that loosens the glass all around, creating two separate elements. We clean it, cut it to the right size and can then reapply it with an improved insulation value.’
That improved insulation value is created by providing one of the glass panes with printed HR coating that insulates better. And the air cavity between the two panes of glass is filled with argon gas. ‘Actually, we have a standard production process for HR++ glass. The only difference is that we do not work with glass coming out of the smelter, but produce with old building materials.’
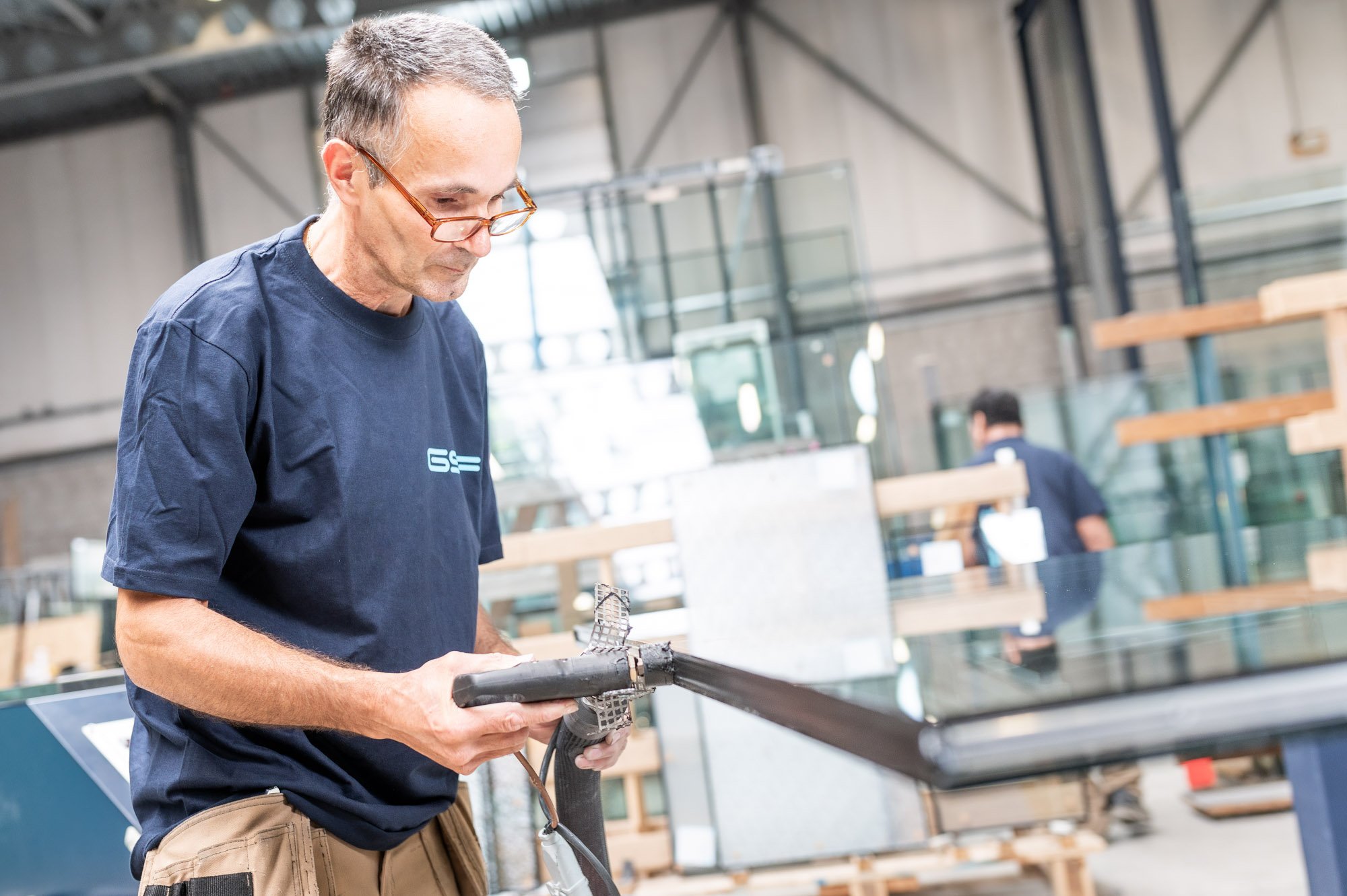
Social and commercial impact
It took considerable investment to bring the circular insulation glass - which GSF Glasgroep sells under the name isoMAX - into production. These included investments in trestles, machinery and new premises. But it didn't hurt the company. ‘Since doing this, we have grown extremely. We now have 60 employees and are entering clients where we might never have entered otherwise. That's something I learned from this: it makes a lot of sense, both commercially and socially, to take a critical look at your business model and adjust it. And with even a small adjustment, you can make a lot of difference.’
‘I am also surprised by everyone's enthusiasm. With clients, but also with employees. I constantly get e-mails from people wanting to join us, because they want to contribute to a nicer way of producing. And perhaps the biggest surprise was that it was so easy. Because what seemed so difficult at the beginning, figuring out whether it could be done, ended up being very easy because of the great interest from universities to research it and clients to apply it.’
72% lower ECI
The research by the Hogeschool van Amsterdam and TU Delft produced, among other things, a life cycle assessment of circular insulation glass. This was only still based on assumptions. ‘When it started to take off, of course we had to provide watertight proof. That's why Alba Concepts made an LCA for us. After that, it's a small effort to be included in the National Environmental Database.’
‘It now turns out that our circular insulation glass has a considerably lower ECI than traditional insulation glass. Our category 1 data comes out to an environmental cost of €1.72 for a lifespan of 30 years. For traditional insulating glass, the ECIin category 2 data comes out to €4.62. I occasionally have glass manufacturers visit me and ask about it. Then it's nice to be able to show such hard figures. There is no discussion about that.’
Equivalent circular glass factory
GSF Glasgroep still has plenty of ambitions. ‘Our circular insulating glass is now about 10% more expensive than traditional insulating glass. That is not much, but for new construction projects it is still sometimes a threshold. In addition, we are of course tied to the harvest we receive. Every year, 400 tonnes of glass are demanded in the Netherlands and 100 tonnes of waste glass are released. So we are not a final solution for the total glass demand in the Netherlands, but we can certainly provide part of it.’
‘Our ambition is to develop a circular glass factory that is equivalent to a traditional glass factory in terms of price and volume. We are already well on our way to achieving this. We are also sure it can be done.’
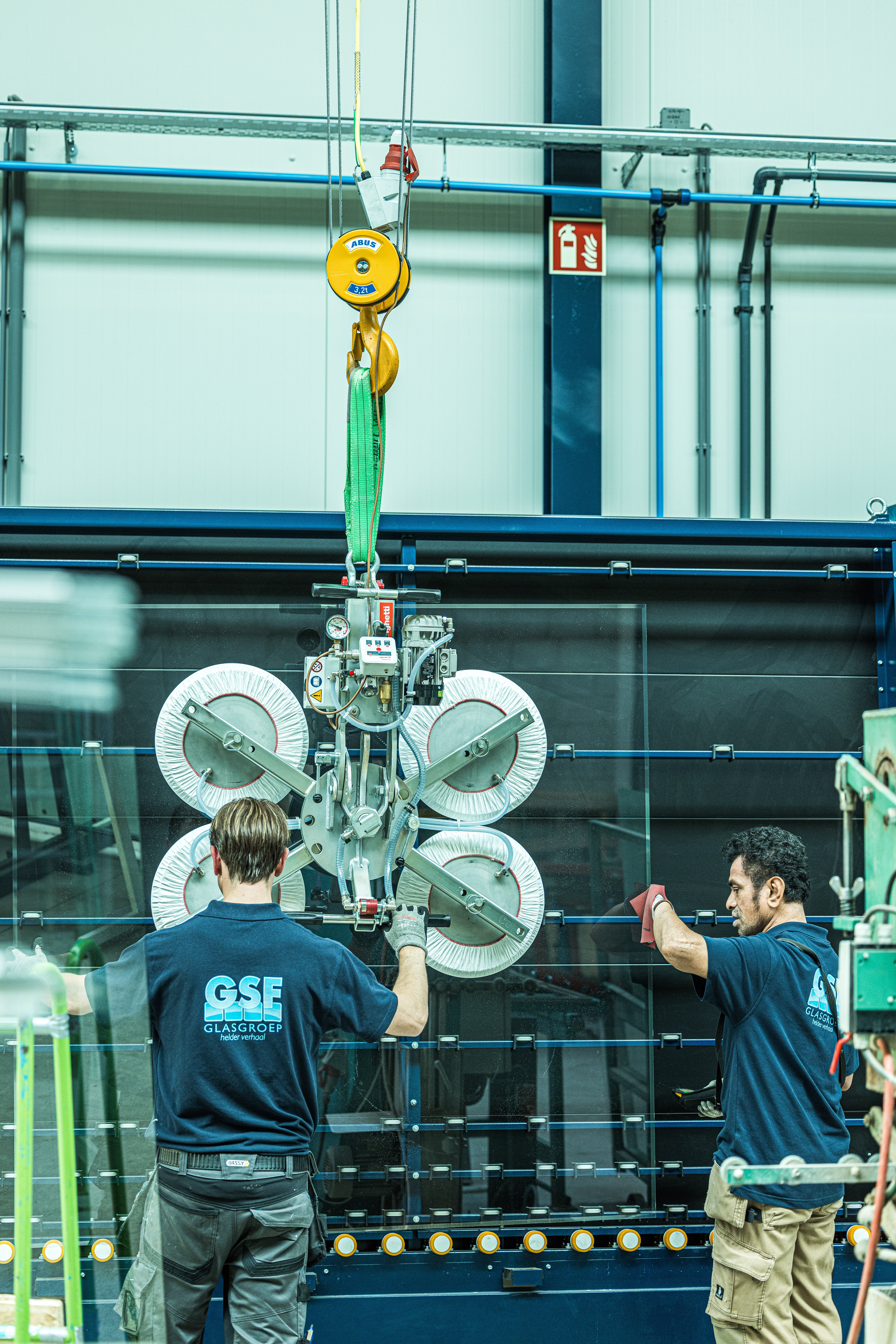
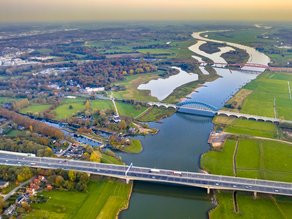
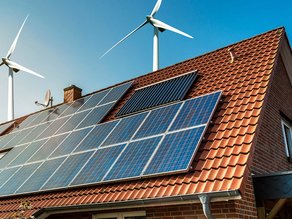
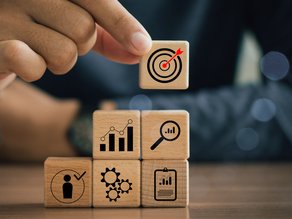
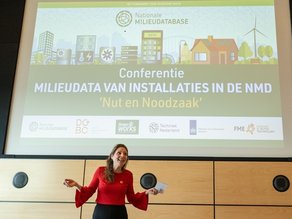