Environmental performance in renovation and transformation
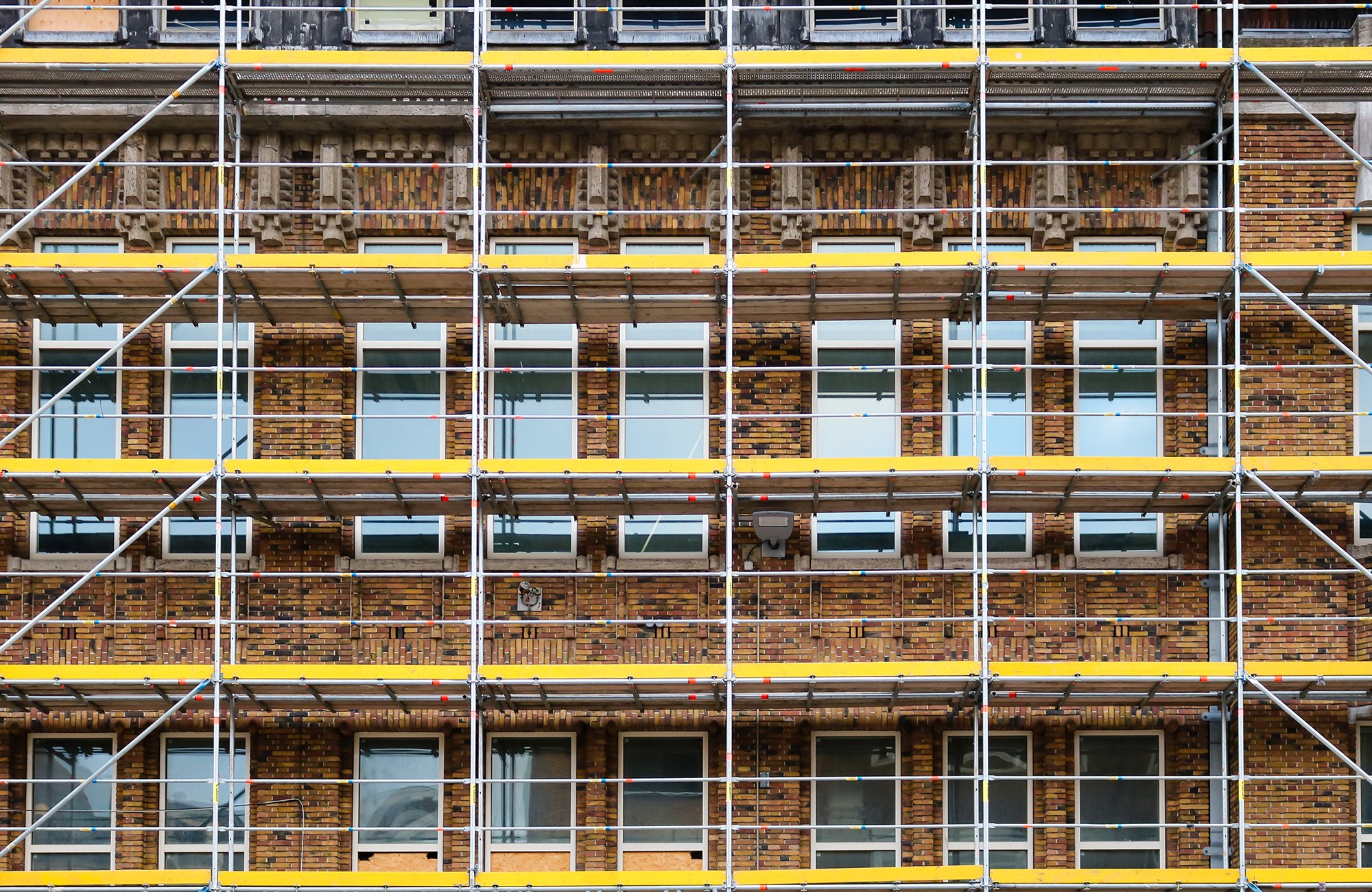
The Netherlands need to become more sustainable, and that means a major sustainability challenge for existing buildings. It makes sense that the environmental impact of the use of materials is also taken into account.
To measure these, the Assessment Method Environmental Performance of Construction Works is available. Since the Assesment Method was developed with new construction in mind, it led to the question of how the Assesment Method can be used for renovations in existing buildings. The research to this end was carried out by W/E consultants and resulted in an addendum to the Assessment Method. A deliberate choice was made for an addendum, because it would be undesirable if a separate calculation method were to arise. The 'Addendum Renovation and Transformation' describes the methodological extension for application in renovation and transformation.
The addendum is meant for projects involving serious renovation where the material state of the building will change significantly. Examples include the installation of new façade at a house and the transformation of an office into several residences. The addendum is not intended for maintenance and light interventions such as the installation of a single dormer.
The methodology focuses on renovations that were not foreseen in new construction and were not included in the original MPG calculation (under phase B5 'Renovation'). This is the case when, in the course of building life, it becomes apparent that a renovation or transformation is necessary to avoid imminent vacancy or demolition of the structure.
This figure shows in a nutshell the MPG calculation for conversion. In the figure, it is assumed that a building built in 1980 with an intended life span of 100 years is remodelled in 2020.
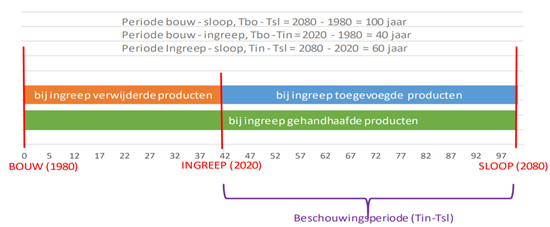
For the environmental performance calculation rebuild, the following products are distinguished and considered:
- the products removed during the operation
- products added during the operation
- products retained during the renovation (products with which nothing is done during the renovation and which remain unchanged during planned maintenance).
The calculation rules of the addendum are based on this distinction. For these 3 types of products, the environmental impact is inventoried and then added up to the total environmental impact (Environmental Cost Indicator (ECI)). Of importance subsequently is the consideration period, as this is the period over which the building ECI is depreciated. For new buildings, it concerns the entire building life cycle (period new construction to demolition). With refurbishment, the situation is different. With refurbishment, it concerns the period from the time of the intervention until demolition. This period is referred to as the residual lifespan.
At the time of the procedure, for the products present in the existing building (which will be removed or retained), the undepreciated environmental impact is determined. This is done on the basis of the ratio between the residual product life and the theoretical product life.
The higher the residual life, the higher the undepreciated environmental burden. If an office facade is replaced after 20 years while the theoretical product life is 50 years, the residual life is 30/50th and the non-depreciated environmental burden is 30/50th x the facade's EQI. With the products to be removed, this 30/50th MKI façade is added to the total environmental burden of the building as an additional environmental burden.
Maintained products also include the non-depreciated environmental burden of the product present. But on the other hand, the product remains functional during its residual life, and the next replacement only comes into play after the expiry of the residual life. As a result, the replacement frequency is less than in the case where a new product had been added during the operation. For a maintained boiler that is 5 years old at the time of the intervention and that has a theoretical lifespan of 15 years, the residual lifespan is 10 years. This means that only 10 years after the intervention the next replacement is needed.
With long-cycle products where the (theoretical) residual life of the product is longer than the residual life of the building, there will be no replacement at all This would be the case, for example, with the façade from the example (residual life 30 years) in the situation where the residual life of the building is 25 years.
After the intervention, there is a new situation and the residual lifespan (and thus the total lifespan) may become significantly longer than foreseen during new construction. The default building life minus the age of the building is then not sufficient.
Extending the residual life can have a positive effect on the ECI of long-cycle products (e.g. an airframe), whose theoretical product life is longer or equal to the residual life of the building. In contrast, if the building life is extended, the number of replacement and maintenance cycles of many (short-cycle) products will increase. This has a negative impact on the overall environmental impact (MKI building).The added products are treated the same as products brought in during new construction. The only difference is the consideration period. For conversion, the consideration period runs from the intervention to demolition; for new construction, it runs from completion to demolition.
The addendum indicates that the aspects below affect the environmental performance
- the achieved building life extension compared to residual life without intervention (longer is positive)
- a larger or smaller GFA after the intervention
- the proportion of 'removed' versus 'maintained' product (maintaining is often positive)
- whether the products are long-cyclic or short-cyclic (in the case of long-cyclic products, the effect of maintaining and extending lifespan is greater)
- the quantity of newly introduced products (more is negative, unless the area of use is also increased)
- the choice of materials when replacing and adding new products (for maintained products, the assumption is that regular replacements will continue with current materials)
The addendum also elaborates on the valuation of reuse and the allocation of environmental impact by product category.
W/E consultants has updated the method for Conversion and Transformation. Practical experience will be gained with it in the coming period. A peer review will also be carried out and the changes will be presented to a advisoryboard. After this, they will be implemented in the addendum and the calculation rules. An update is expected to be available by the end of 2024.