Voorbij Prefab:
“Making concrete more sustainable is not that complicated; it's a mindset.”
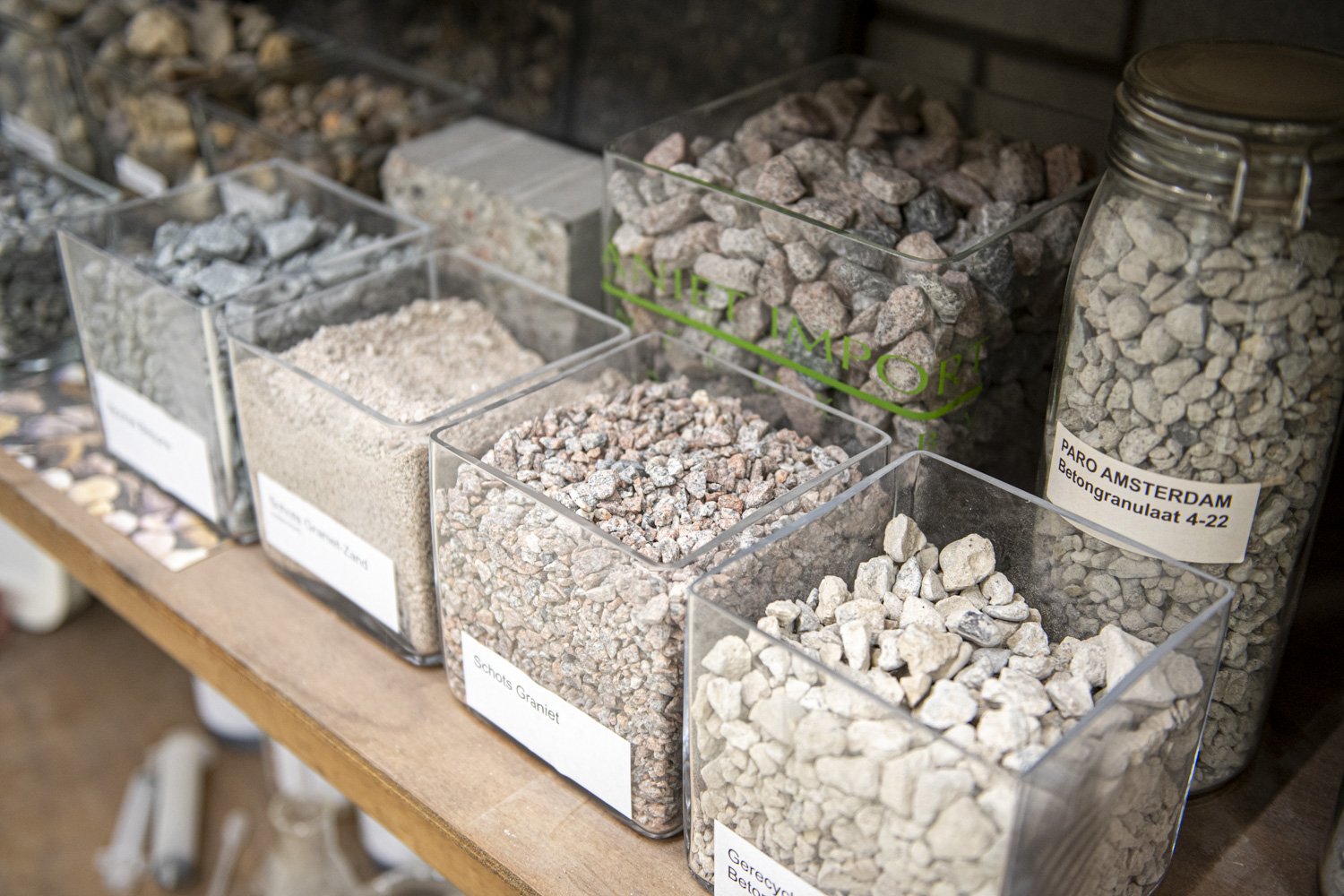
Since December 2024, Voorbij Prefab's thick concrete walls have joined its thin concrete walls in the National Environmental Database with category 1 data. Since January 1, 2021, the Amsterdam-based company has been pouring all its shells with what it calls CO2-low concrete, which meets the definition of “dark green” in the concrete agreement. The development of and transition to this more sustainable variant of concrete (40% less CO2) took the company only six months, and innovations have continued to follow one another ever since. Voorbij Prefab continuously shares its insights with the industry, as it does in this interview. “If you look at what is possible instead of thinking about what is not possible, you suddenly discover that a lot more is possible.”
Voorbij Prefab was founded in 1935, when Cor Voorbij established his company Voorbij's Beton in Wilnis. The company grew into a high-tech prefab concrete factory with 130 employees, located in the Western Port Area of Amsterdam.
For this interview, we spoke with Niki Loonen, sustainable concrete specialist at TBI, the group that Voorbij Prefab has been part of since 1996. And with Ruud Out, concrete technologist.
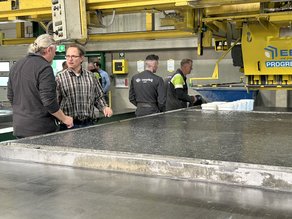
Sustainability specialist TBI
Niki Loonen
Concrete shame?
Niki tells us that he has been working with concrete for 26 years and has been actively involved in making it more sustainable for the past seven years. “We noticed that concrete was increasingly being talked about in negative terms. A kind of ‘concrete shame’ arose. Yet concrete is a fantastic building material. You can do so much with it. At the same time, I also understood where the criticism was coming from.”
“What I wanted was to avoid getting caught up in a yes-no debate and instead work together to see what could be improved. I wrote a blog about it, which ended up on the desk of Dorien Staal, then director of Voorbij Prefab.”
“We shared the ambition to make concrete more sustainable more quickly, sat down together, and six months later we had concrete with 40% less CO2 emissions. Making concrete more sustainable isn't that complicated; it's a mindset. If your goal is clear and you look at how it can be done instead of thinking about what can't be done, suddenly a lot more becomes possible.”
A matter of courage and action
Niki makes it sound as if it took no effort at all, but that's not entirely true. “Of course, it doesn't happen by itself. It's a matter of courage and action. And cooperation. Because if you think you can do something like this on your own, you're completely wrong. There are so many stakeholders involved! The only way is together.”
Evolution instead of revolution
Niki knows that this applies to both external partners and internally. “You're going to make changes to a production process that has been the same for a long time. You have to involve people in that. For example, we had been working for years with a certain formwork strength, the strength that the concrete must have in order to be removed from the mold. We wanted to see if we could reduce that formwork strength, one of the factors that is important for working with a more sustainable concrete mix.”
“First, you think it through carefully with the structural engineer, then you test it in the lab, and then you do a controlled pilot in the factory. If the pilot is successful, you increase the volume a little, then a little more, and so on, until it becomes the new normal. We involved our colleagues in all these steps. It doesn't happen all at once. With innovation, you can choose between an evolutionary or a revolutionary approach. Evolution generally works better.”
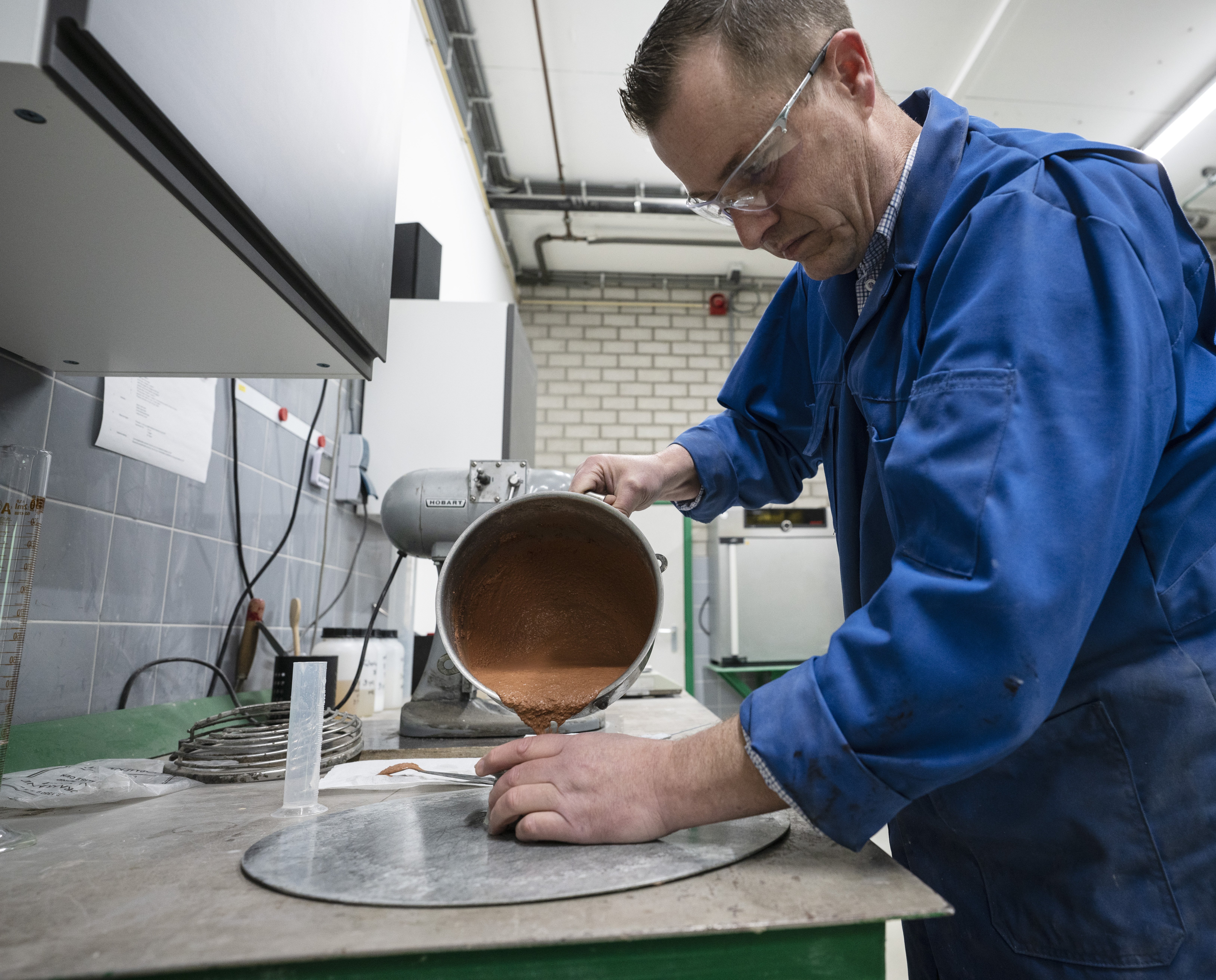
Making low-CO2 concrete
What makes Voorbij Prefab's concrete low-CO2 is the concrete mixture. Ruud Out, concrete technologist at Voorbij Prefab: “The basis for concrete is cement, and what's great about cement is that it reacts quickly. That's what you want with prefab concrete, because then you can reuse the mold quickly. However, cement is also CO2-intensive. So we had to find something we could add to the concrete so that we needed less cement, but the concrete would still harden quickly. That addition was alkali activation, a component of geopolymer technology.”
50% recycled concrete granulate
Niki had also been working on this technology for some time. “With the activator (Alkine), we achieve the required concrete strength in the same amount of time. We also save cement by using more blast furnace slag (a by-product of Tata Steel, among others) than usual. We also use 50% recycled concrete granulate that comes directly from our neighbors, recycling company Renewi.”
“A lot has to be done to adapt a concrete mixture like this. The certifier has to approve it, the mixer, the concrete technologist, the mixing installation has to be adapted, and the aforementioned formwork strength has to be reduced. And you can see all kinds of obstacles along the way. Will the concrete remain strong enough, will it crack, will it dry quickly enough? But by involving everyone in the process and taking it step by step, we manage to do it all relatively quickly.”
Insight into your impact
Both the thin walls for ground-level homes and the thick walls for apartment buildings from Voorbij Prefab are now listed in the National Environmental Database with category 1 data.
Niki: “By collecting your environmental data, you gain a very good insight into the impact of the materials you use. Of course, we already knew a lot, for example about steel and cement, but you also see that transport to the construction site has a significant impact. And that the impact of your own processes – solar panels on the roof, electric vehicles, LED lights in the office – is relatively low. That doesn't mean we don't invest in those things—you have to do everything you can—but removing a kilo of cement from our concrete has a much greater impact.”
Making sustainable design choices
“That's why it's so important for all manufacturers to gain this insight. Where is my impact, how do I compare to others, how do I ensure that I can keep up with the pack or even become a leader? In addition, this data naturally provides input for building designers. If you are designing a building, you want to know: should I make the door handles more sustainable or get to work on the concrete structure? That is only possible with good data.”
Towards zero-impact concrete
Low-carbon concrete is now on its way to becoming the standard in the industry. “We haven't applied for a patent. If we see something that works, we share it so that others can use it the next day. We want to become more sustainable, and that goes much faster if we do it together. In 2025, we're going to do some really cool things that will radically reduce the impact of our concrete. We're really moving towards zero-impact concrete. As soon as we know exactly how it works and whether it works, we'll share it with the industry right away.”
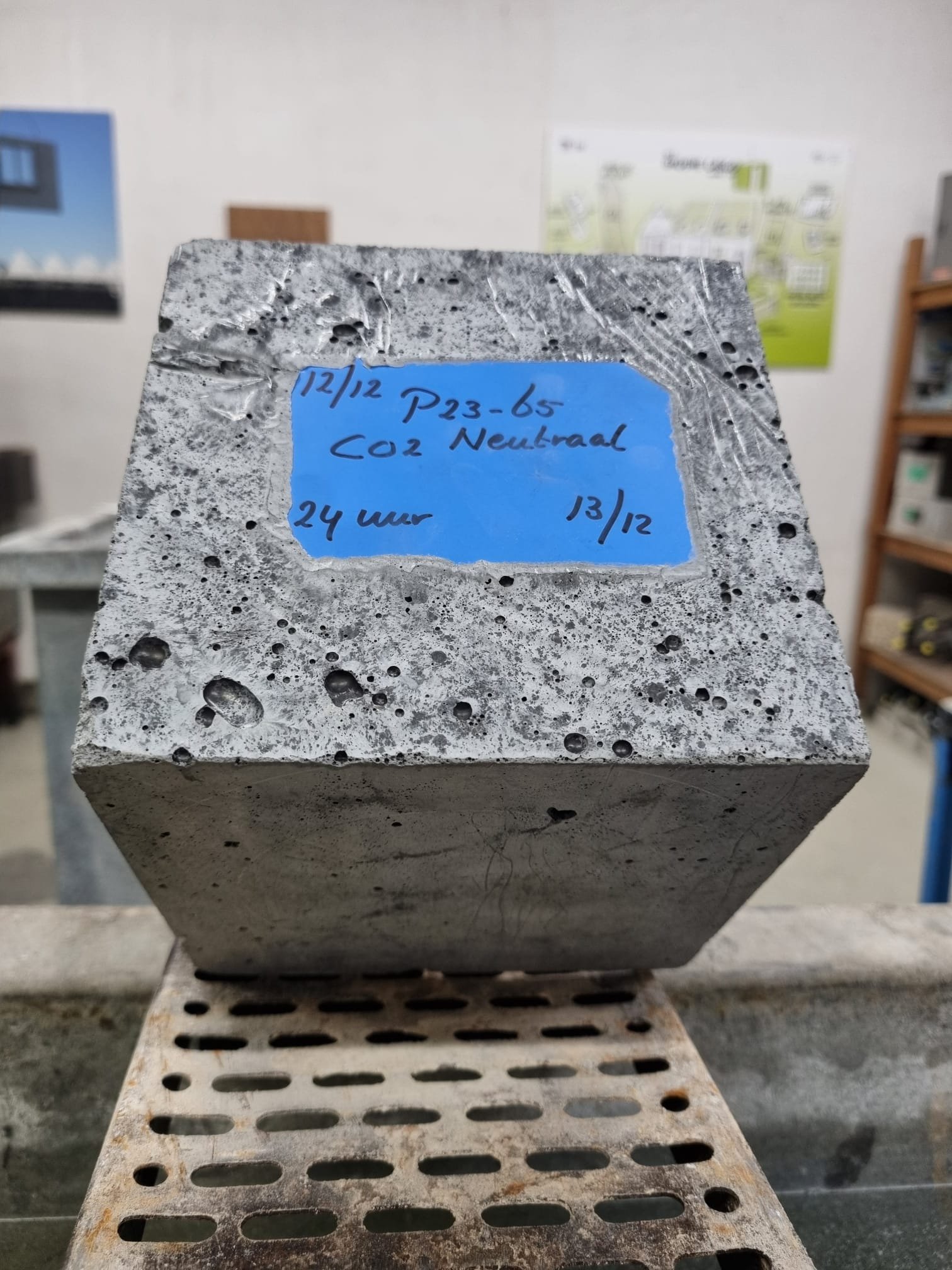