CircuFloc cardboard wool now in the NMD
ECI: €0.02 for a 75-year lifetime
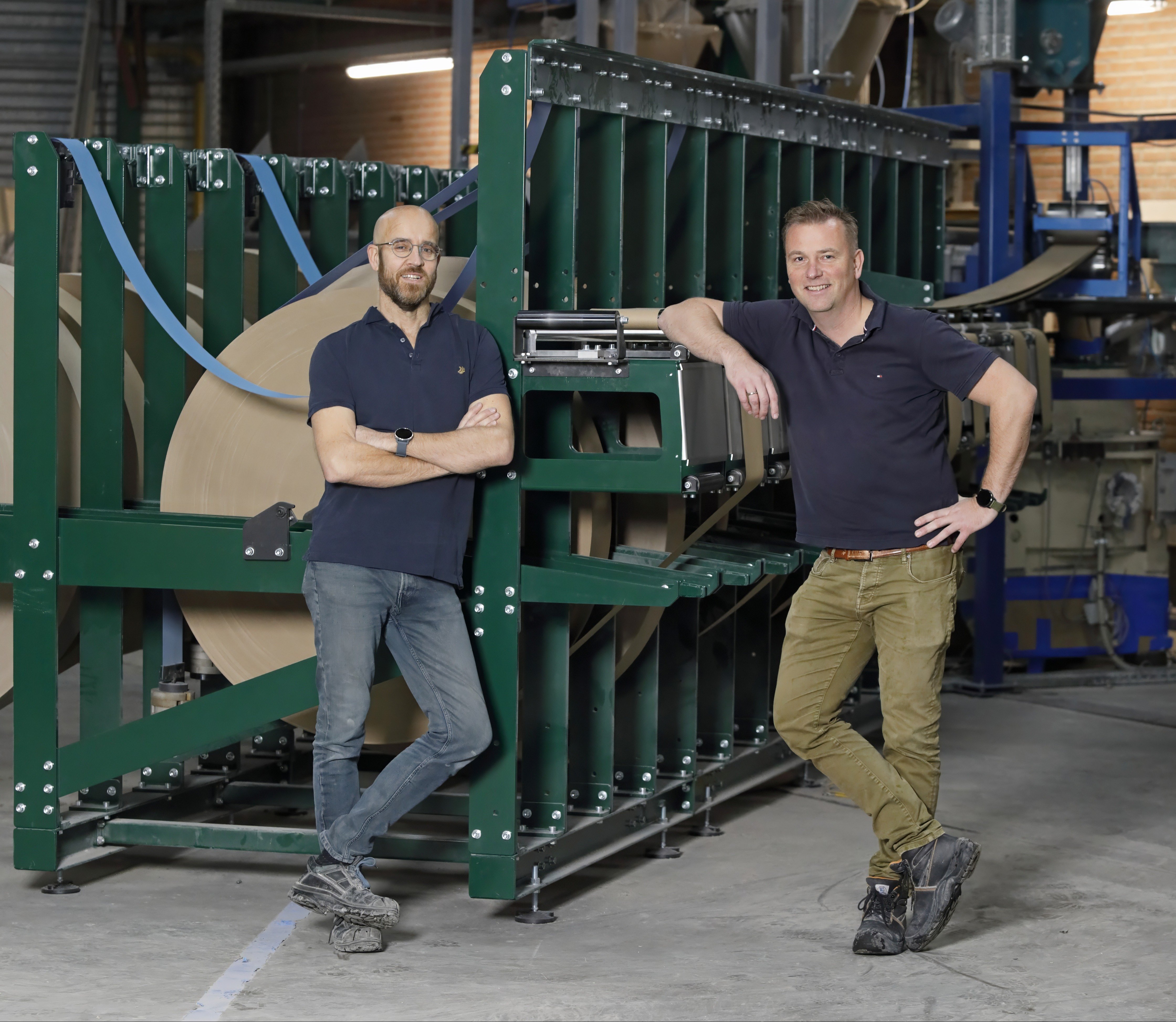
Over the years, his focus there shifted increasingly to finding the best use for residual flows. One of those uses turned out to be the application of paper waste streams as insulation material in the construction industry. He decided to develop the idea himself and when he told his rowing mate Jan Tabak about it, they founded a company together. Now they have a patented technology to turn reject rolls of cardboard paper into insulation material with a very low ECI. An interview about entrepreneurship, just going out and trying and the will to do the right thing.
We speak online for this interview, but Wouter and Jan do sit together at the computer at their production site in Brummen. Here they talk about how their company CircuSol Insulation came into being two years ago, after Wouter had actually been walking around with the idea of making insulation material from reject rolls from the cardboard production process for ten years.
Lots of unused waste material
Wouter: “There is a huge flow of reject products in the paper industry. When moving from one type of paper to another, for example, there are always rolls that don't meet specifications. Those residual rolls or residual streams sometimes go back into the process or are sold. As filling material for boxes, for example.”
“The efficiency in the paper industry is very high, but because so are the volumes and the requirements for reuse are often quite strict, there is always a percentage of residual streams that are 'left over.' And even if that percentage is only 1% of the total, the large volumes make that very interesting.”
CircuSol: “Residual stream for one is raw material for another.”
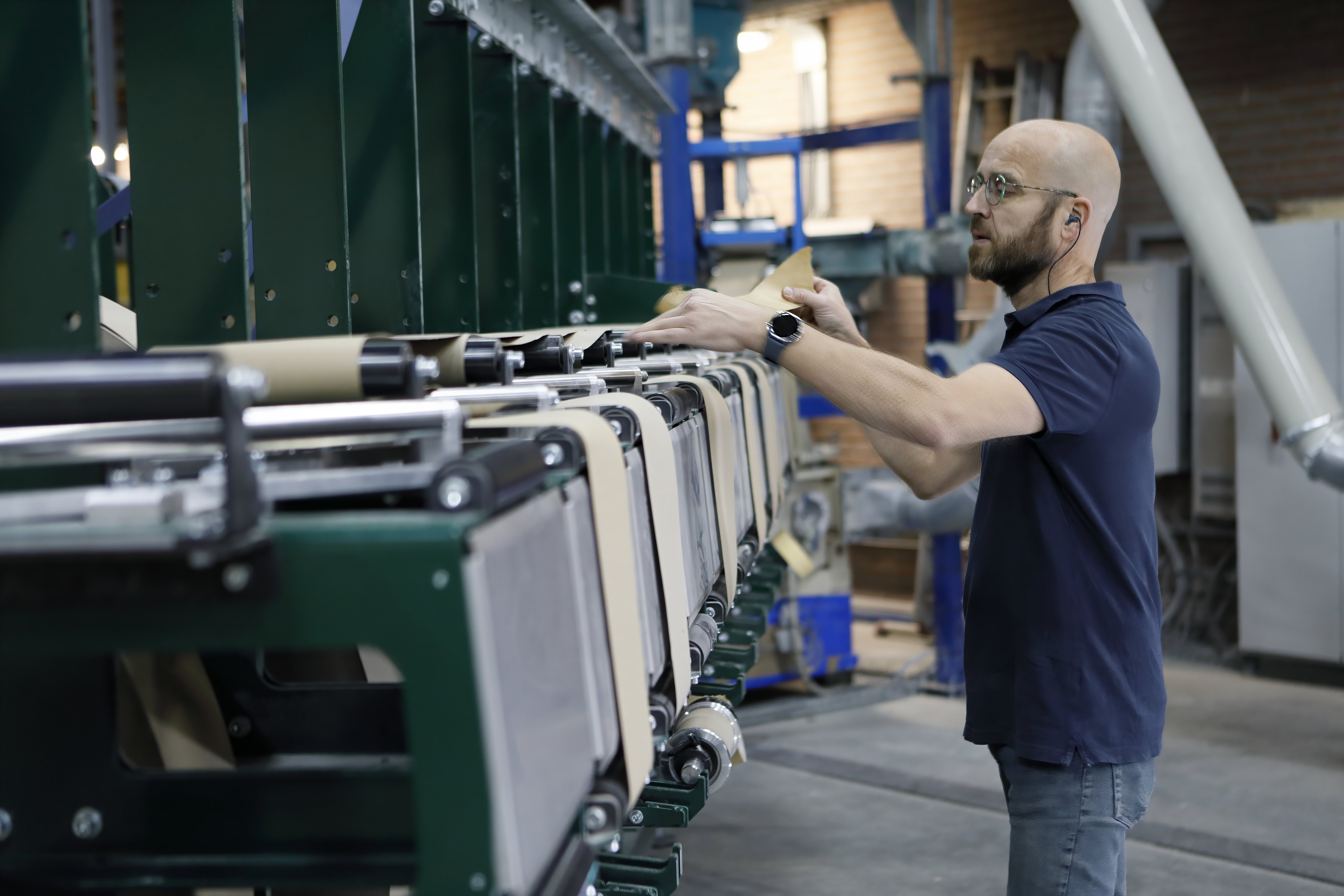
Biobased insulation material
Wouter thought that more should be possible with these waste streams. His search led him to the idea of making insulation material from cardboard waste streams. Research into this showed that it should certainly be possible, but his idea did not find an ear in the paper industry. “They wanted to stick to their core business,” he said. Wouter couldn't let go and told anyone who wanted to hear about his idea. That included Jan Tabak.
Exploring opportunities further
Jan: “I had just moved to Deventer and joined a rowing club to meet new people. I ended up sitting on the bench in that rowing boat next to Wouter and he kept talking about that big stream of cardboard paper. When we were in the car together one day on our way to a competition, the conversation turned to how we could actually complement each other business-wise perfectly.”
“Wouter is a real tech guy, I had been working at a large dairy company in marketing and sales for years at the time. I know chain thinking, marketing products is my specialty and the sustainability and chain thinking of Wouter's idea really appealed to me. That day, there in the car, we shook hands and decided to explore the opportunities for this product together.”
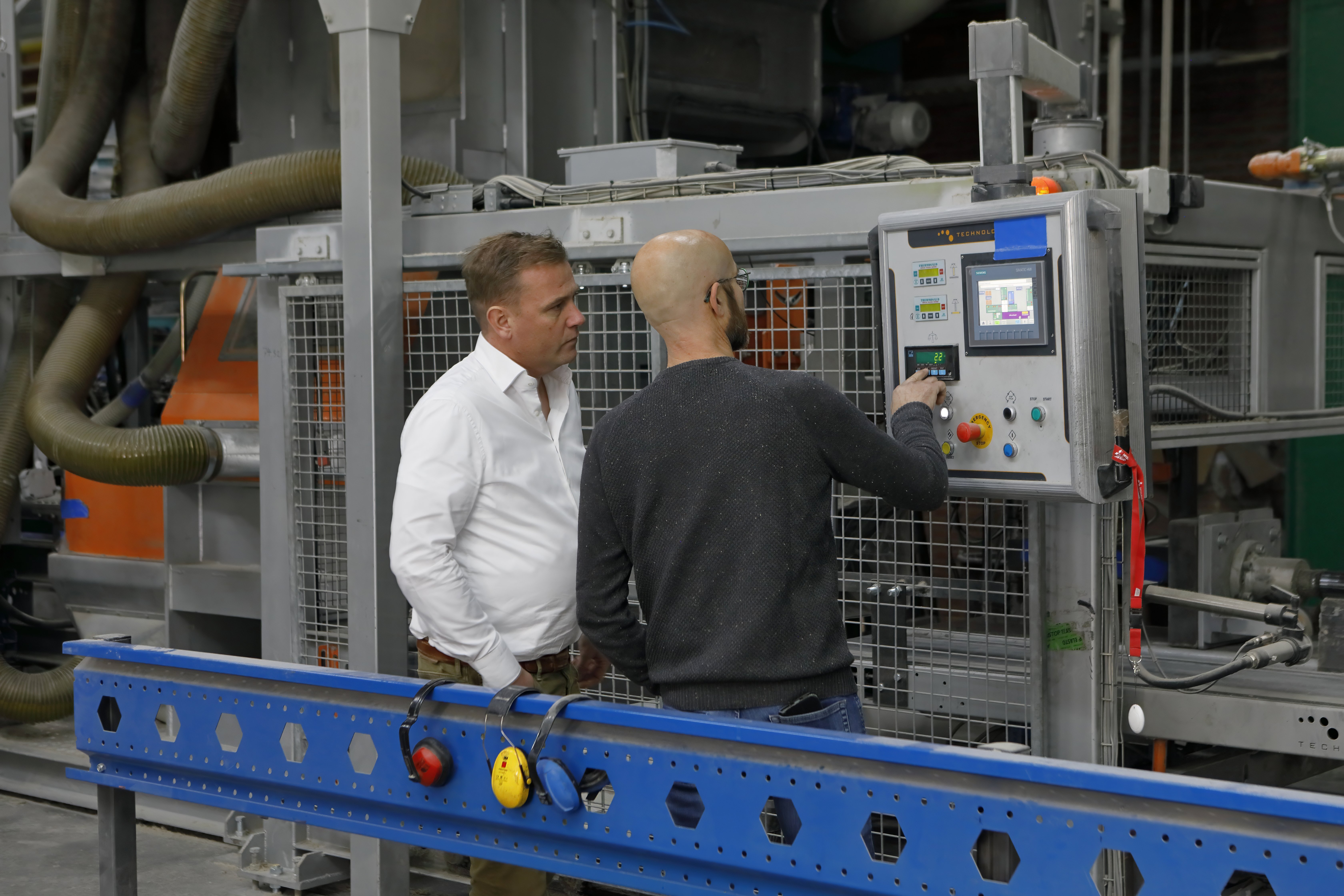
Growing supply, growing demand
Those opportunities turned out to be great. Jan: “Insulating with cellulose has existed for a long time, of course, but mainly old newspapers and magazines are used for that. This flow of residual materials is decreasing rapidly - almost halved compared to 30 years ago - because more and more people read their newspapers and magazines online. In contrast, the stream of residual materials in cardboard is large (51.1 MiO tons) and is a growing market (47% larger than 30 years ago). We have more and more stuff delivered to our homes and it often comes in boxes. In addition, cardboard paper mills are well spread across Europe and there are very many of them. So this raw material is everywhere.”
Wouter: “On top of that, the construction industry is paying more and more attention to bio-based building. Consequently, the demand for biobased insulation materials is also growing. We decided to tie the knot and both quit our well-paying jobs. That was the beginning of CircuSol Insulation.”
Money and machines needed
What followed was an exciting period: how do you go about developing such an idea? What do you need to test it? “We came into contact with Warmteplan, a company that has been active in biobased insulation for 35 years. They are especially specialized in applying the materials. Blowing in wood fiber and cellulose, which foils to use where, Lambda values, stability, the building physics aspects. We had a click and they had a production line they weren't doing anything with. We entered into a long-term cooperation in which we complement and strengthen each other.”
What also helped enormously was a grant from the Circular Factories Incentive Fund. “We had to provide a well-founded circular business plan for that. Well, we had that. We received the maximum grant amount.”
Testing, testing and: succeeding
So Wouter and Jan had a production site and the financial clout to actually start making the product. “We both come from multinational companies. As a result, we both knew the Stage Gate development process: if it's not good enough, you don't have to go on endlessly. Cutting off and stopping should also be possible. So that's also how we entered that period of testing and trial.”
Getting both the product and the production good and stable was, of course, the goal. And that succeeded. “We now have a patented technology with which we can achieve the same stability and insulation value with a very low density as other insulation materials. Cellu
Enthusiastic reactions
The first reactions from the market are positive, Wouter and Jan tell us. “Our product is biobased and free of harmful binders. It is fully circular as well as form-free, making it applicable in almost any interior space. It has fire class E, making it a natural insulation material with good fire resistance.”
There is also work to be done: “Construction in the Netherlands is very used to working with insulation mats. In other countries, blow-in insulation material is already much better known. Blown-in insulation is much faster (about 3 to 5 times faster), provides 100% seamless filling and has no cutting waste. It is a very fine way of insulating in both new construction and renovation.”
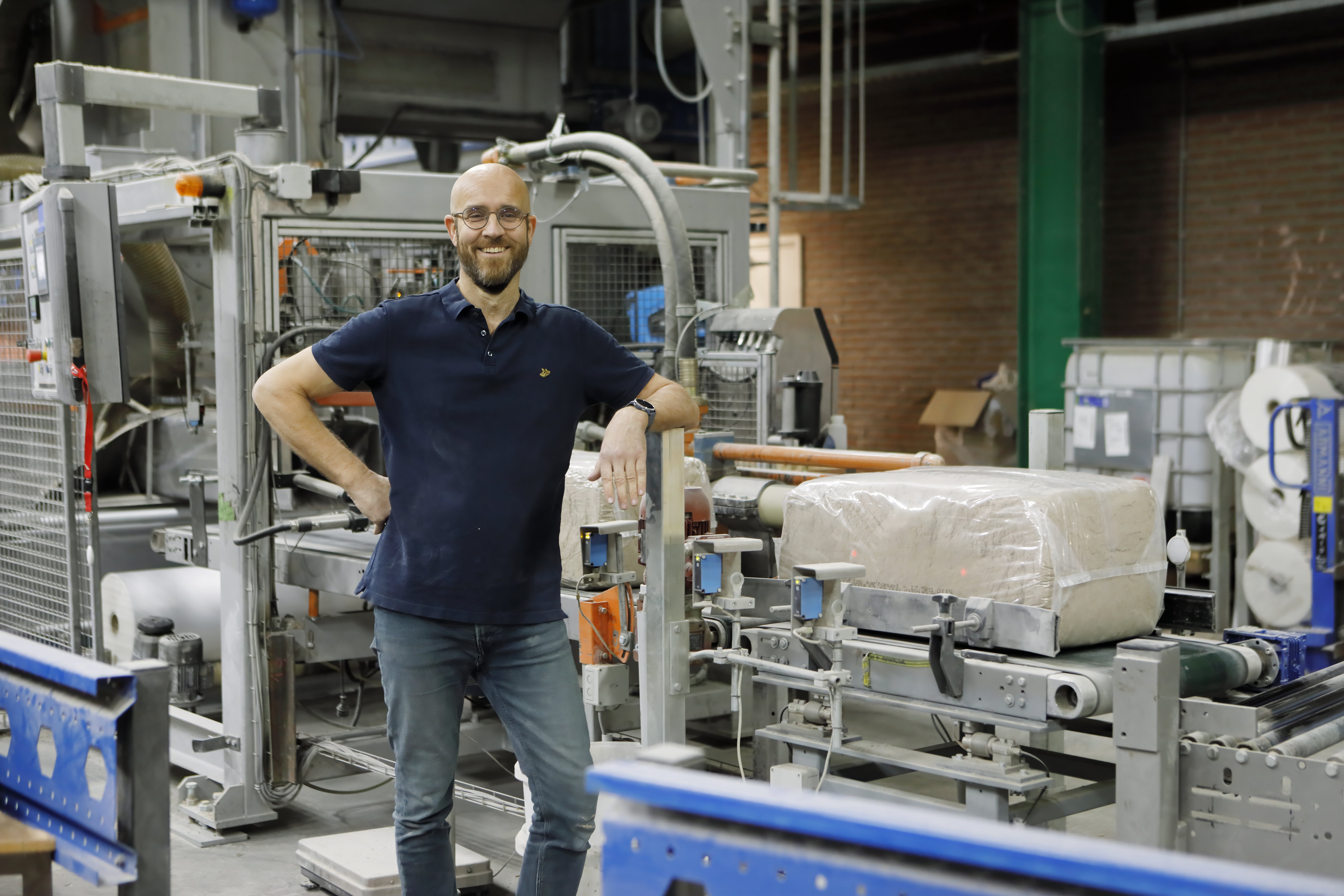
ECI of €0.02
What helps CircuSol Insulation tremendously now in making their biobased insulation material better known is that the ECI also confirms how environmentally friendly the CircuFloc cardboard wool product is. “With help from the reimbursement scheme White Spots from the National Environmental Database, we had a life cycle analysis done. That LCA allowed us to have CircuFloc Cardboard Wool included in the NMD with category-1 data. The ECI subsequently turned out to be even lower than we thought, at €0.02 for a 75-year lifetime. This makes CircuFloc Cardboard Wool the insulation product with the very lowest ECI in the Netherlands. That opens doors at companies and that's what we need as a startup.”
Wouter and Jan also used the LCA to keep looking for improvements. “We did a stress test, looking at what happens to the ECI if we make adjustments in the production process. Can we still cut the ECI in half? We are now in talks with TNO about this.”
1st 100 homes with cardboard wool insulation
Looking back, developments have been rapid over the past two years. “We have really achieved a lot: a patented technology, a factory making a certified product, a lot of interest from the market ánd concrete projects; the first 100 homes have been insulated with bio-based CircuFloc cardboard wool insulation. That makes us proud and we look forward to the time to come.”
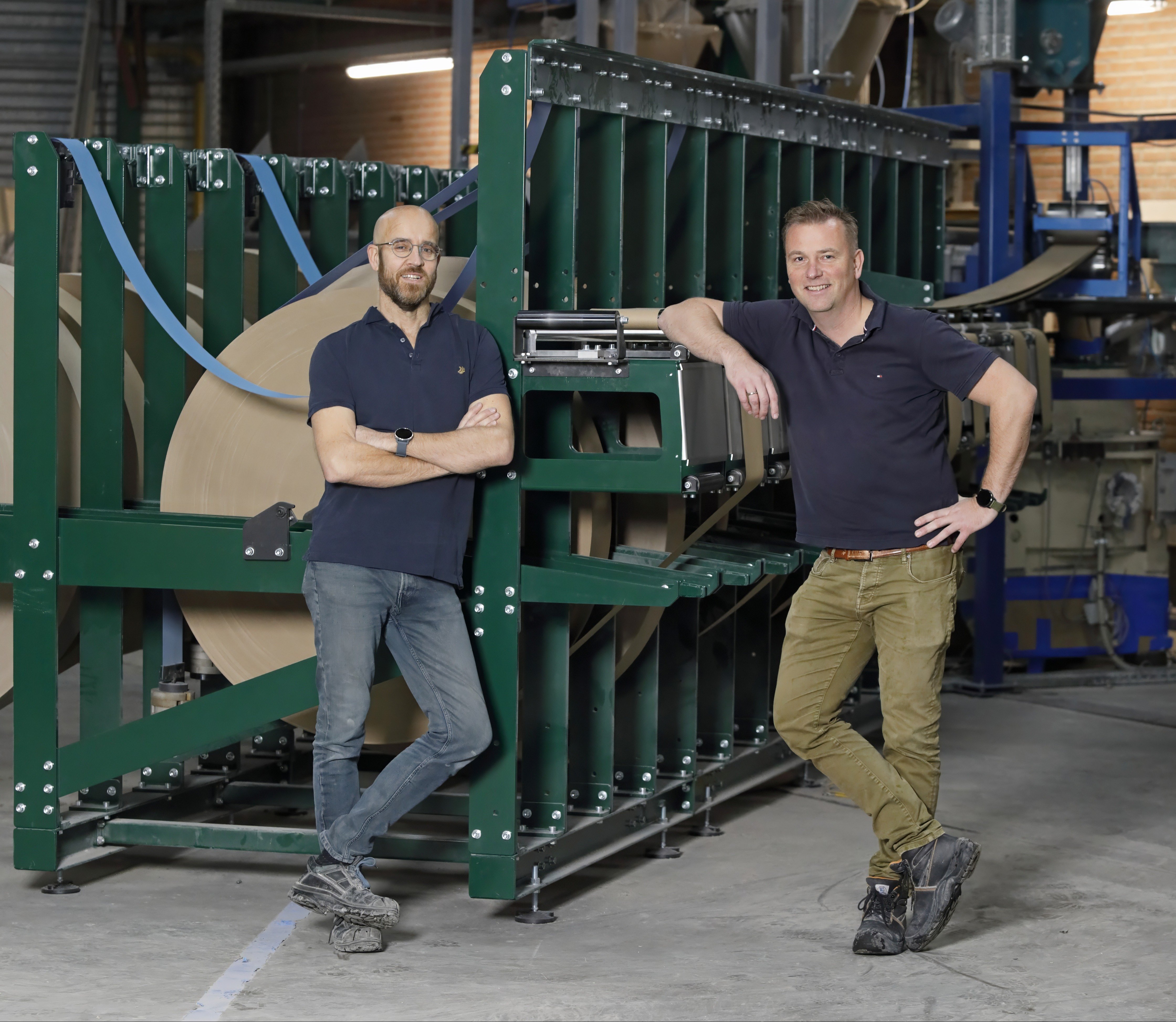
Lees meer
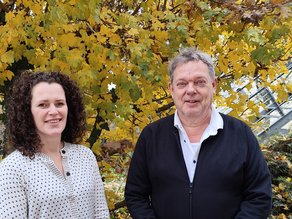
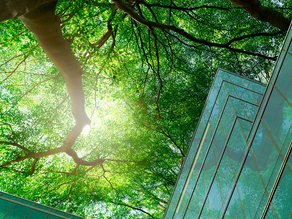
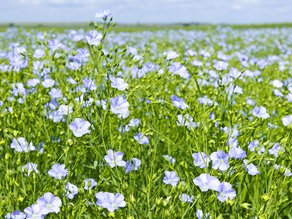
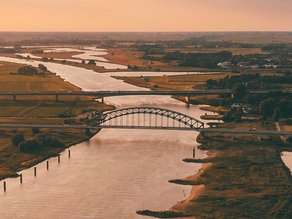