Bamboo siding from FelixWood with category 1 data in the NMD
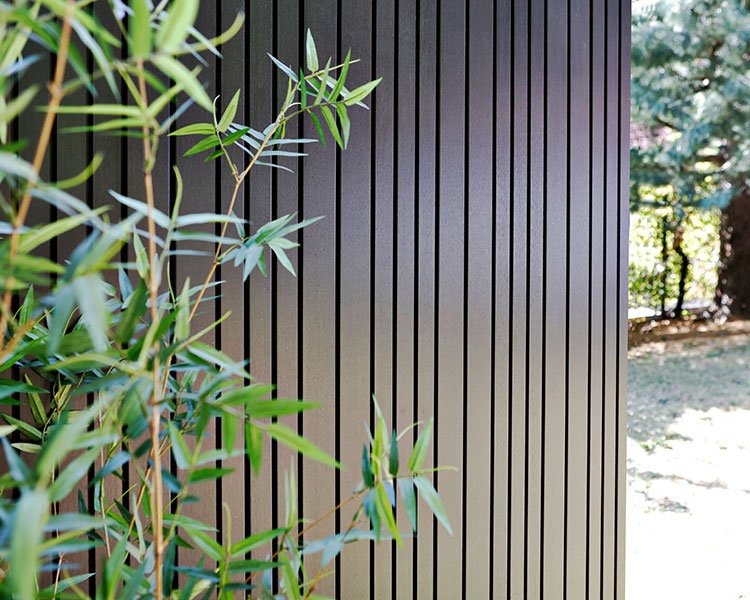
The history of the Felix company goes all the way back to the year 1891, when Felix Clercx founded a sawmill in Mierlo. For a long time, the focus was on importing exotic wood species. This changed in the nineties with the launch of FelixWood. The company used this brand to start developing its own products such as decking, garden furniture, fences and siding. Two of these products – FelixWood Symphony and Melody, both bamboo façade components (thermally modified) – are now listed in the NMD with category 1 data.
Deputy director Sander Kindt talks about what it is like to change from a trading company to a company with its own brands and product development. And how the family culture and always having an eye for the next generations is a guiding factor in the choices Felix makes.
From trader to brand company
“We started out as a timber company, but that changed when we were taken over by Forestia in 2019 and decided to start developing our own brands and products. We have three house brands: FelixWood® (for wood and bamboo), Fiberdeck® (wood-plastic composite) and Cobra® (fasteners and clips).
“This is a huge step for our company. We now have a Research & Development department and a product management department, and we work together with producers who manufacture products exclusively for Felix according to our own specifications and quality standards. With these three brands, we focus on the applications decking, fencing and cladding.
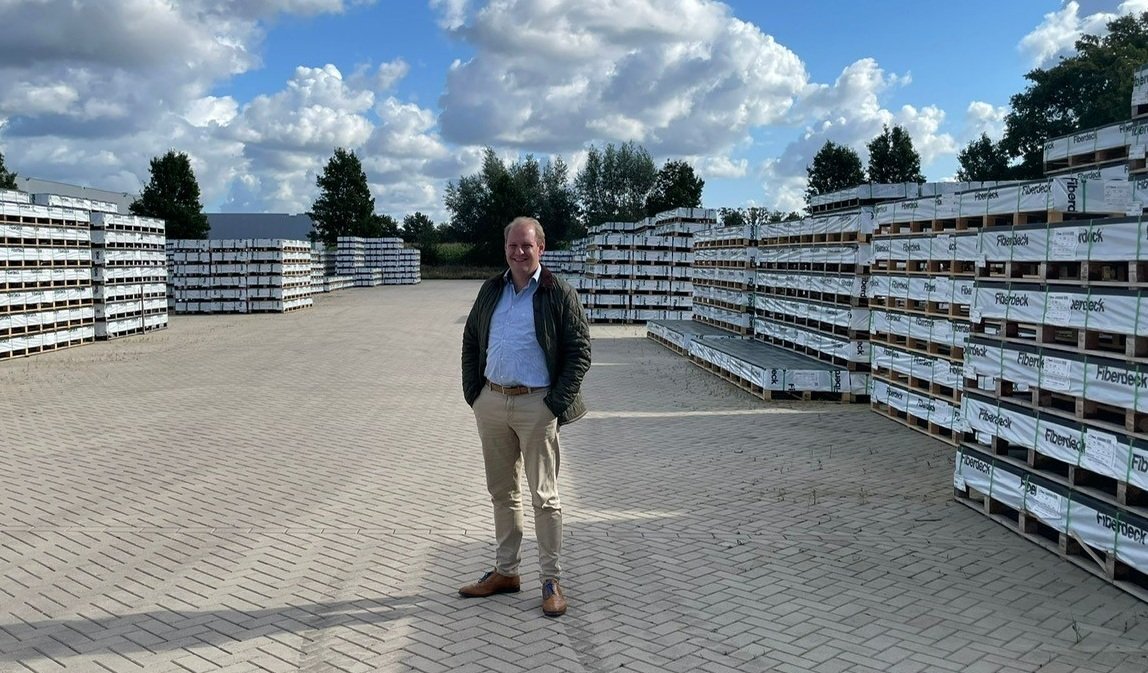
Matching decking and façade components
“With the network in the wood industry that we already had, we came into contact with bamboo suppliers a lot. Bamboo is a wonderful product. It is strong, easy to work with, grows super fast and also stores CO2 during its growth. That makes the material very sustainable in use.”
“We started developing bamboo products for the garden, such as decking boards. The bamboo is thermally modified for our products. Thermal modification gives it a different color and makes it harder and more stable. Gradually, we noticed that customers also wanted siding made of the same material. They like the idea of having a deck board with the same profile on the outside of their house.”
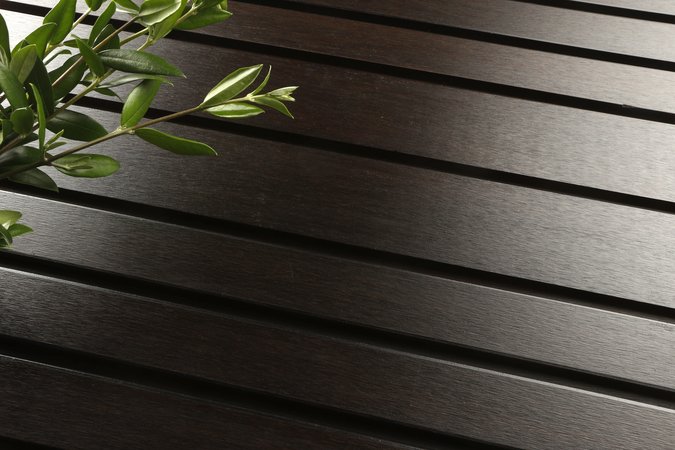
A process of trial and error
It was not easy, the transition from a trading company that sells brands from other suppliers to a company that develops and sells its own brands, says Sander. “We really went on a journey of discovery together. There is so much to consider. Design, appearance, processing, installation method, fire class. There were moments when we thought: what have we gotten ourselves into? But the feeling of pride is even greater when we succeed. Some beautiful products have already come out of it.”
Complete concept
Two of these products are now listed in the NMD with category 1 data: our Symphony bamboo siding (with fire rating C) and Melody. Both are made from thermally modified bamboo.
“We supply these products including Cobra® mounting materials, because not only is quality very important to us, we also want to offer something that is easy to work with. We developed a system with clips for this purpose. This means you don't have to be a carpenter to install our products; anyone can build with them.”
Collecting data for the LCA
For inclusion in the NMD, Felix naturally had to have a life cycle analysis made of the products. “That turned out not to be very complicated thanks to the good and close cooperation with our partners. We set high standards for our suppliers and work closely with them. We have also had them independently audited for years, so we already had access to all the processes.”
“This is very important, especially when you do business with companies in Asia. Not only for the environment, but for the whole picture of corporate social responsibility. For this reason, we have an office in Malaysia with our own staff to keep the lines of communication short with our sawmills and production locations for bamboo and WPC. We have a good view of how things are going there. That is something we, as a family business, find very important.”
Knowledge from the LCA
Despite the insights Felix already had, the company also learned a lot from the LCA. “We import our products from far away. We thought this had a major impact on the environmental costs, but now we see that production accounts for 80-90% of the environmental costs and not the logistical movements.”
“Bamboo is already being cultivated in Europe, but suitable production facilities are not yet in place and the supply is not yet large or competitive enough. On the other hand, we can already influence production. We choose suppliers who are consciously concerned with sustainability and renewability. For example, those who use renewable energy and renewable raw materials. It also goes without saying that our wood is FSC certified and complies with the European Timber Regulation (EUTR) and, by 2025, the stricter EU Timber Regulation (EUTR). Good management of the forests where our wood and bamboo come from is our top priority.”
Even more products in the NMD
Felix is currently working on collecting data for even more LCAs, including for the WPC (wood plastic composite) range of their Fiberdeck® brand.
“These products are marketed under our Fiberdeck® brand and are made of 95% recycled material. We are curious about the MKI of these products, although that is not the main reason we are doing this. We believe that as a producer you should be honest and transparent about what you do, so that people can make good choices. Conscious choices, because they have insight. We therefore hope that as many producers as possible will have their products and materials included in the NMD.”