Aesthetic solar facades from Solarix with category 1 data in NMD
What started in 2012 with an initial idea about combining aesthetics and solar panels is now a company with 20 employees that has already provided more than 15 projects with designer solar facades.
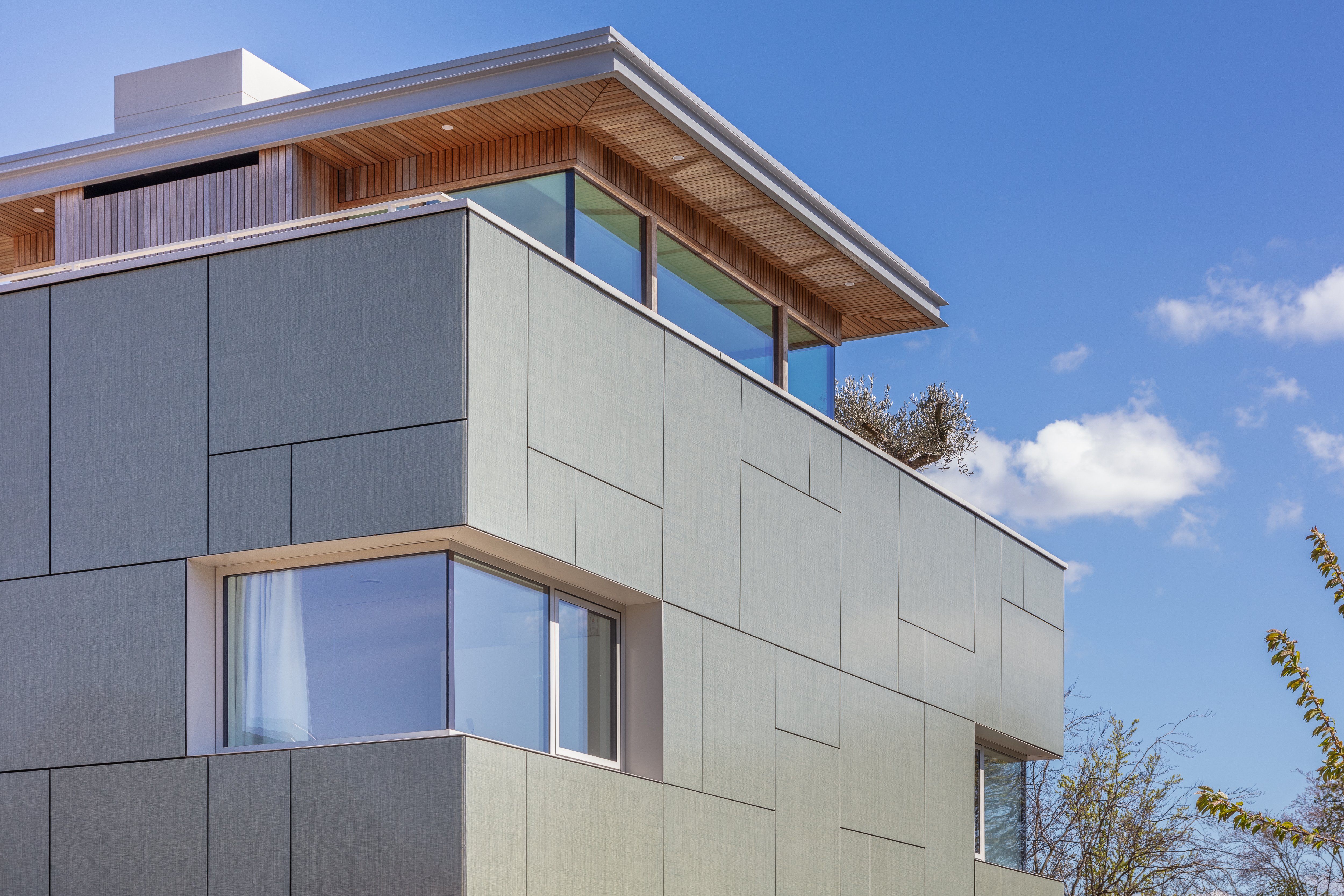
Architect Marloes van Heteren and product designer Reinier Bosch founded Solarix in 2016 because they believe that making the world more sustainable is faster with more attention to aesthetics. Moreover, if we want to accelerate the energy transition “we need to use not only the roof, but also the facade as an energy source.” Solarix recently completed an initial product LCA. We talked about it with Marloes van Heteren and project leader Alissa Labeur.
Marloes calls in for our chat from the De Kikker project. This primary school in Osdorp is getting a thorough renovation of its poison-green facade, with panels from Solarix. The façade is now expected to generate 67,000 kWh per year. Marloes says she likes the fact that this is a primary school. "We are showing what is possible. Or better yet, what should be normal. Our children will start asking us: ‘Why did you ever make facades without solar panels?’"
Getting started with LCAs
Alissa Labeur calls in from the office. She talks about another project recently delivered, namely DSM's new headquarters in Maastricht. Both the roofs and facades of this building feature solar panels. This project, says Alissa, gave Solarix the final push to start working on something that had been on the wish list for some time: making a life cycle analysis of the solar façade panel.
"DSM wanted to have category 1 data on the sustainability of the product for the facade panel we are applying to their building. Since we were already planning to do a life cycle analysis, that was a great opportunity to use this facade panel as a starting point. We decided to do a training course at Rethink to learn how to do LCAs ourselves. Very interesting and we gained a lot of knowledge from it, also about our product and processes."
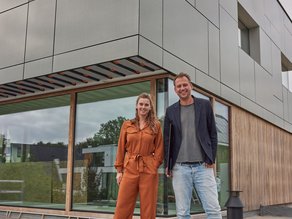
Marloes van Heteren and Reinier Bosch
Solarix zonnegevels
Different requirements than for roof panels
Before we talk more about that, it might be good to explain how Solarix's product is put together. Marloes: ‘Our solar facade panels are different from the standard solar panels you put on a roof. Other requirements also apply, for example for rigidity, fire class and stability. Our facade panels consist of two layers of tempered glass without a frame."
"The fastening system is also different, partly because different aesthetic requirements apply to a facade than to a roof.For this, we developed our own ‘invisible’ mounting system, which also allows the panels to be individually removed from the façade."
New design and new colours
What further makes Solarix's façade panels unique is the design. "We do not imitate existing façade materials such as marble and bricks.We focus on new design and new colours. That was - and still is - a matter of doing a lot of research into types of ink, colour perception, transparency and, above all, finding the optimum of colour perception and energy yield. Recently, we did a test with pigments that give another higher yield."
Manufacturing process continuously sustainable
In recent years, for instance, Solarix developed 78 different panel designs, a unique colour technology and a patented mounting system. And that research continues. Just like the search for opportunities to make the production process ever more sustainable.
Alissa: ‘Making life-cycle analyses helps us with this. What we did notice with this first LCA: many parties are not ready yet. As a result, collecting data from our suppliers was not easy. Fortunately, you can always fall back on the values that are already known for the elements that make up our product. Although at times this also led to interesting discussions. For instance, what about the lifespan of a solar panel versus the lifespan of a facade panel? A solar panel has a shorter lifespan (25 years) than a facade panel (75 years), how do we deal with that with our solar facade panels?"
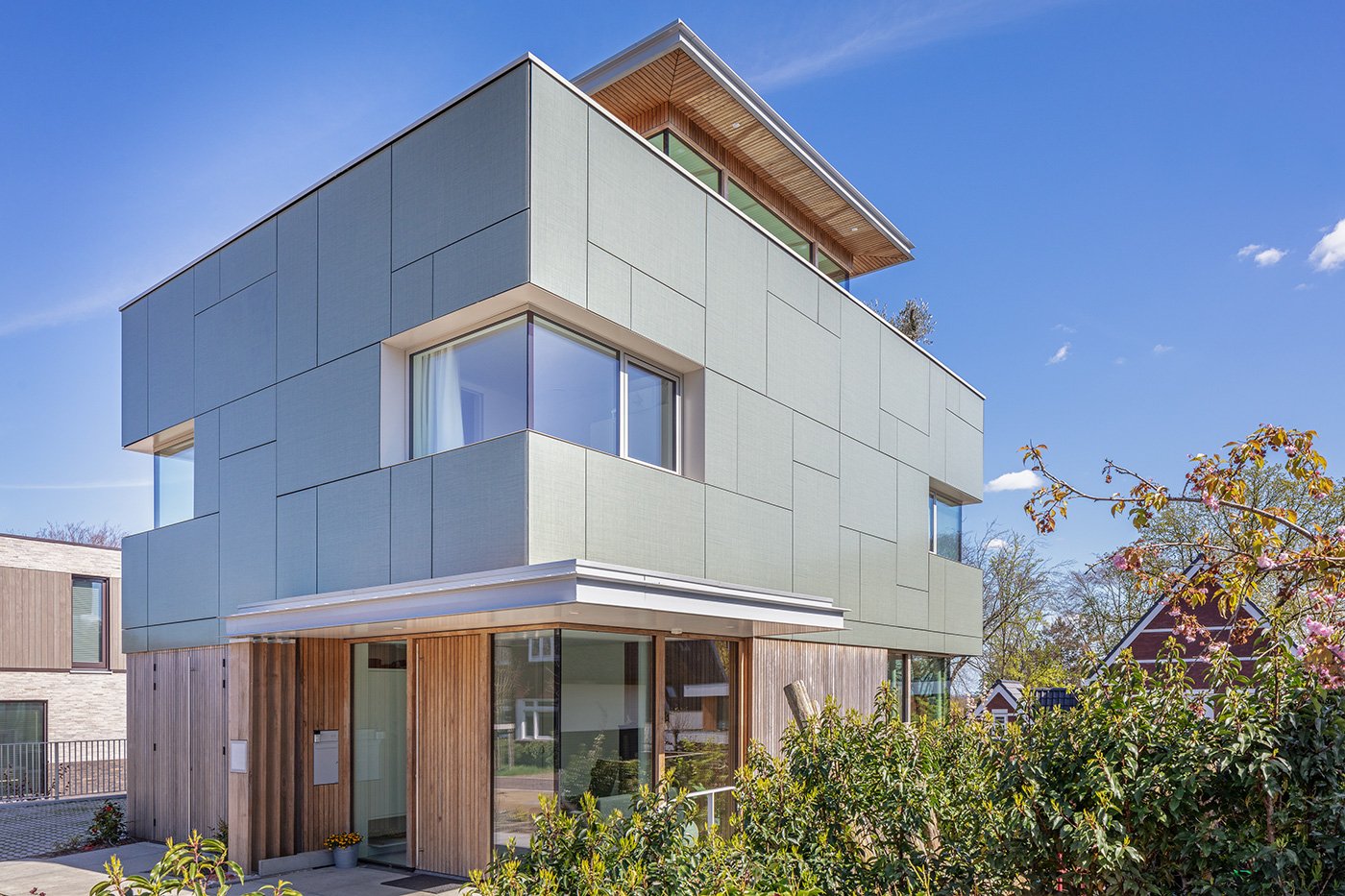
Different transport, better score
"The timing of making the LCA is also quite a decisive choice with us, we noticed. We are developing our product and processes all the time. For instance, we used to pack the façade panels in a kind of wooden crates. The idea was to reuse those crates, but that didn't always work out. So we changed the way we transport the façade panels. We now transport them lying down, with reusable corner pieces.Those corner pieces are very flexible in use and always come back, so we can use them for multiple deliveries.As a result, we already have another better score than in our first LCA. We are very happy with the score."
Less material, more recycling
Recycling and optimisation is something Solarix is constantly working on. "We now use aluminium for our mounting system that is 80% recycled. And by mounting smarter, we save material. In that respect, we are curious about the next LCA. We have already made all kinds of nice improvements."
Balancing interests
Marloes also mentions the adhesive layer in the panels: the encapsulant. "We are constantly researching types of adhesives we can use to bond the mounting system to the panels. Ideally, of course, we choose the most organic encapsulant possible, but in this we also have to take into account regulations around fire safety, for example. We cannot choose an adhesive that does not comply with the right fire class. It's a balancing act of interests."
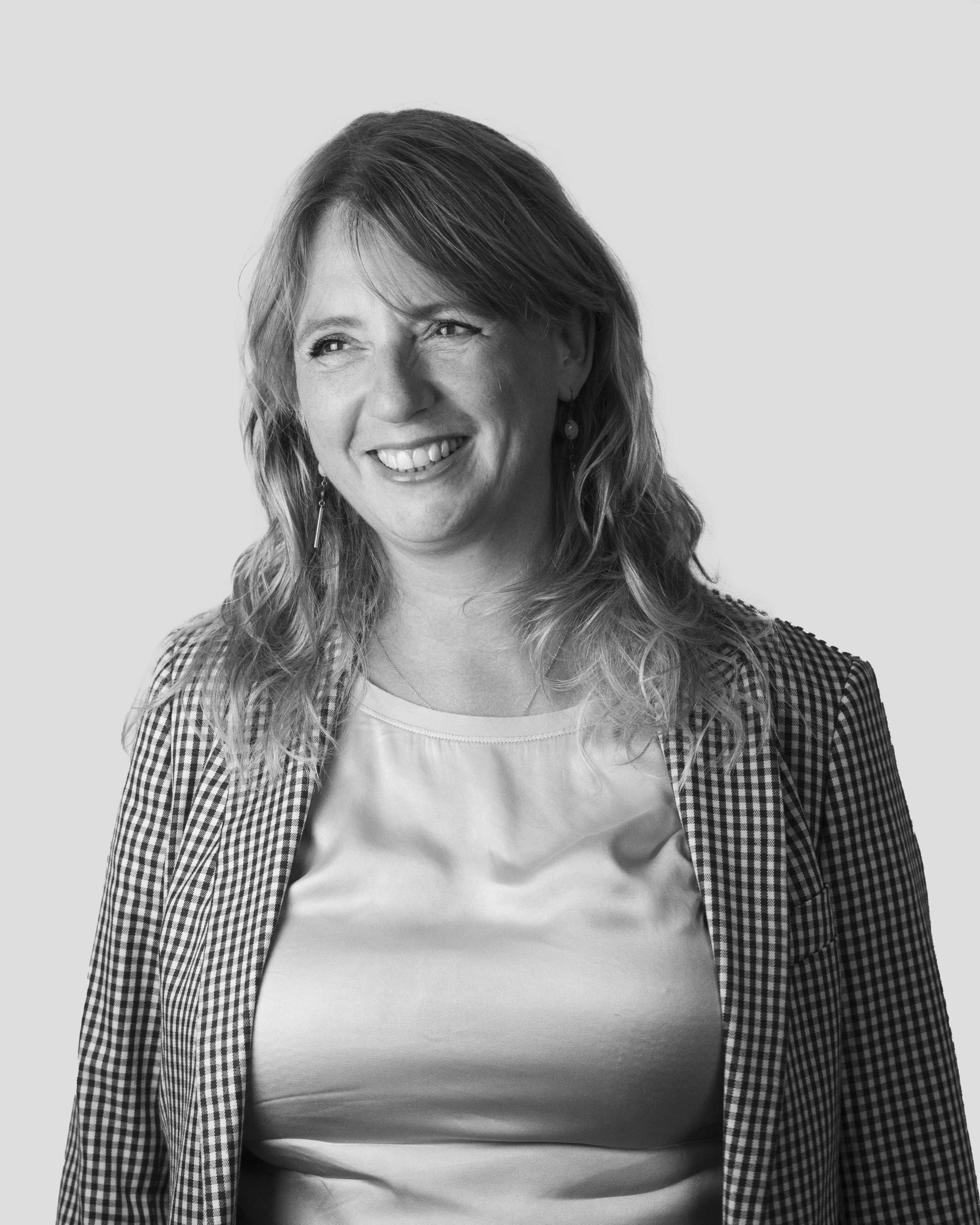
Understanding products and processes
Marloes and Alissa recommend it to every producer to get started with LCAs."You gain much more insight into your own product and processes, especially if, as we do, you draw up the LCAs yourself.It also allows you to tweak it.Looking at what happens where with the score, which changes have a lot of impact or little."
Solarix also recommends inclusion in the NMD with category 1 data. Marloes: ‘We started this in early 2023 and at that time hardly anyone was talking about it. Now, a year later, we often get questions from clients whether we have LCAs and EPDs."
The start of more
Alissa: ‘Now many companies already work with the NMD, because it is a good way to factor sustainability into your material choices. In the future, only more companies are going to use it, there's no way around it. That is why we are going to calculate more products. Now the NMD contains the panel we used for DSM's project.With the type of cells, the type of ink and the materials in it. The next step is to make an LCA of our standard custom products. Once we have that category 1 data, we will of course have that included in the NMD as well."
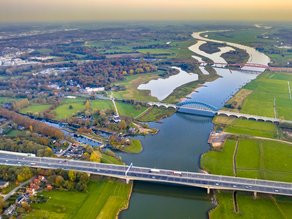
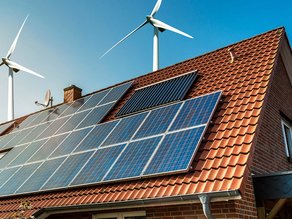
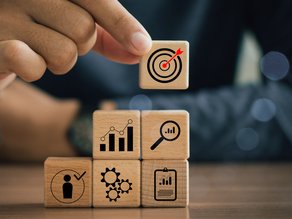
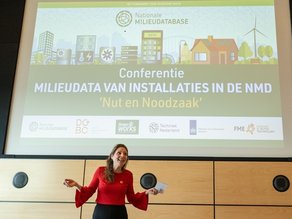