GSF Glasgroep maakt hergebruikt isolatieglas: “Op naar een gelijkwaardige circulaire glasfabriek”
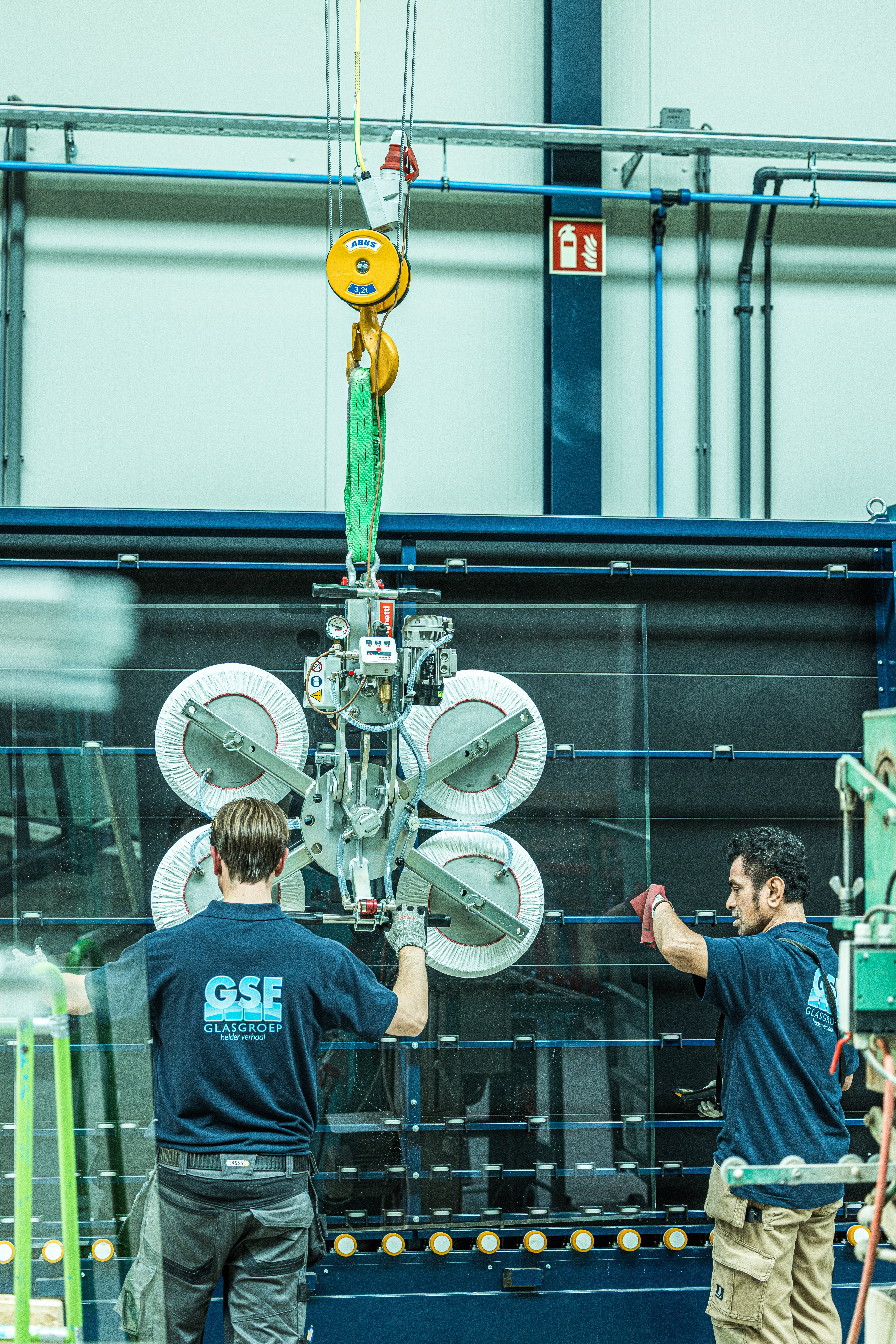
Ongeveer drie jaar geleden, middenin de coronacrisis, besloot GSF Glasgroep te onderzoeken of isolatieglas op zó’n manier hergebruikt kan worden, dat het de hoge isolatiewaarde behoudt. Het antwoord bleek: ja, dat kan. Inmiddels staat het circulaire isolatieglas isoMAX Circutherm 50 ook met categorie 1-data in de NMD. De MKI blijkt 72% lager dan traditioneel isolatieglas. Directeur Maarten Rood: “Ons doel is om een circulaire glasfabriek te ontwikkelen die gelijkwaardig is aan een traditionele glasfabriek. Zodat we qua prijs en volume vergelijkbaar worden met traditioneel isolatieglas. Die kant gaan we al op.”
Maarten startte zo’n 15 jaar geleden met werken bij het glasbedrijf van zijn ouders. Een traditioneel glasbedrijf dat heel lokaal actief was in en rondom Lelystad. In 2015 nam hij het bedrijf over en werd hij directeur.
“Gaandeweg gingen we meer werken voor overheids- en semi-overheidsorganisaties. Gemeenten, woningcorporaties, verzekeraars, de NS. Uit die hoek kwam de laatste jaren steeds vaker de vraag hoe we de CO2-uitstoot van ons materiaal konden verlagen. Glas is een van de meest heftige bouwmaterialen als je kijkt naar de CO2-uitstoot van de bouw of renovatie van een huis of gebouw. Zo kwam bij ons de vraag op: kunnen we het niet gaan hergebruiken?”
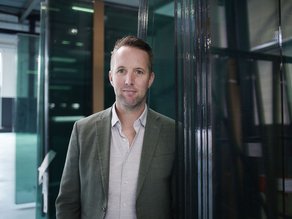
GSF Glasgroep
Maarten Rood
Wetenschappelijk onderzoek
“We zeggen in Nederland eigenlijk altijd al dat glas wordt hergebruikt. Dat is ook zo. Ik denk dat we in Nederland misschien wel een van de beste recyclingsystemen hebben van de wereld. Maar wat daarbij gebeurt is dat het glas weer de oven ingaat en gebruikt wordt voor bijvoorbeeld flessen en glaswol. Hergebruik van de ruiten als geheel, dat gebeurde nooit. De gedachte was ook dat dit niet mogelijk was voor isolatieglas. Omdat een bestaande ruit daarvoor te vervuild is.”
“Nu besloten wij het toch te gaan onderzoeken. Dat konden we niet alleen. Wij hebben veel verstand van glas, weten goed waar je het kan krijgen en hoe je het kan toepassen. Maar van sterkteberekeningen hebben wij weinig verstand. En wat zou hergebruik doen met de isolatiewaarde van het glas op de lange termijn?”
Een samenwerking met de Hogeschool van Amsterdam en de TU Delft bood uitkomst. “En het mooie was, door de coronacrisis was er meer dan genoeg ruimte in de agenda om dit onderzoek te doen. Dus wij leverden glas aan en de universiteit kon vervolgens met behulp van klimaatboxen onderzoek doen. In een paar maanden tijd werd zo gesimuleerd wat het effect zou zijn na 20 jaar. Zo werd duidelijk dat je bestaande ruiten prima kan gebruiken om weer isolatieglas van te maken.”
Circulair productieproces
De volgende stap: daadwerkelijk gaan produceren. “We kwamen er al snel achter dat bestaande producenten dit niet wilden oppakken voor ons. Dus besloten we zelf een productielocatie op te zetten.”
GSF Glasgroep zamelt sindsdien zelf gebruikt glas in; het oogsten. “We investeerden in bokken om het glas meteen als het uit een woning of gebouw komt, veilig en heel te bewaren en transporteren. Dus glas dat niet stuk is, maar wel vervangen moet worden omdat het niet meer voldoet aan de isolatiewaarde, wordt niet meer in de container gegooid, maar gaat naar onze productielocatie. Daar beschikken we over een grote machine die het glas rondom losmaakt, zodat er twee losse elementen ontstaan. We maken het schoon, snijden het in de juiste afmeting en kunnen het vervolgens weer toepassen met een verbeterde isolatiewaarde.”
Die betere isolatiewaarde ontstaat door een van de glasbladen te voorzien van geprinte HR-coating die beter isoleert. En de luchtspouw tussen beide glasbladen wordt gevuld met argongas. “Eigenlijk hebben we een standaard productieproces voor HR++-glas. Het enige verschil is dat wij niet werken met glas dat uit de smeltoven komt, maar produceren met oude bouwmaterialen.”
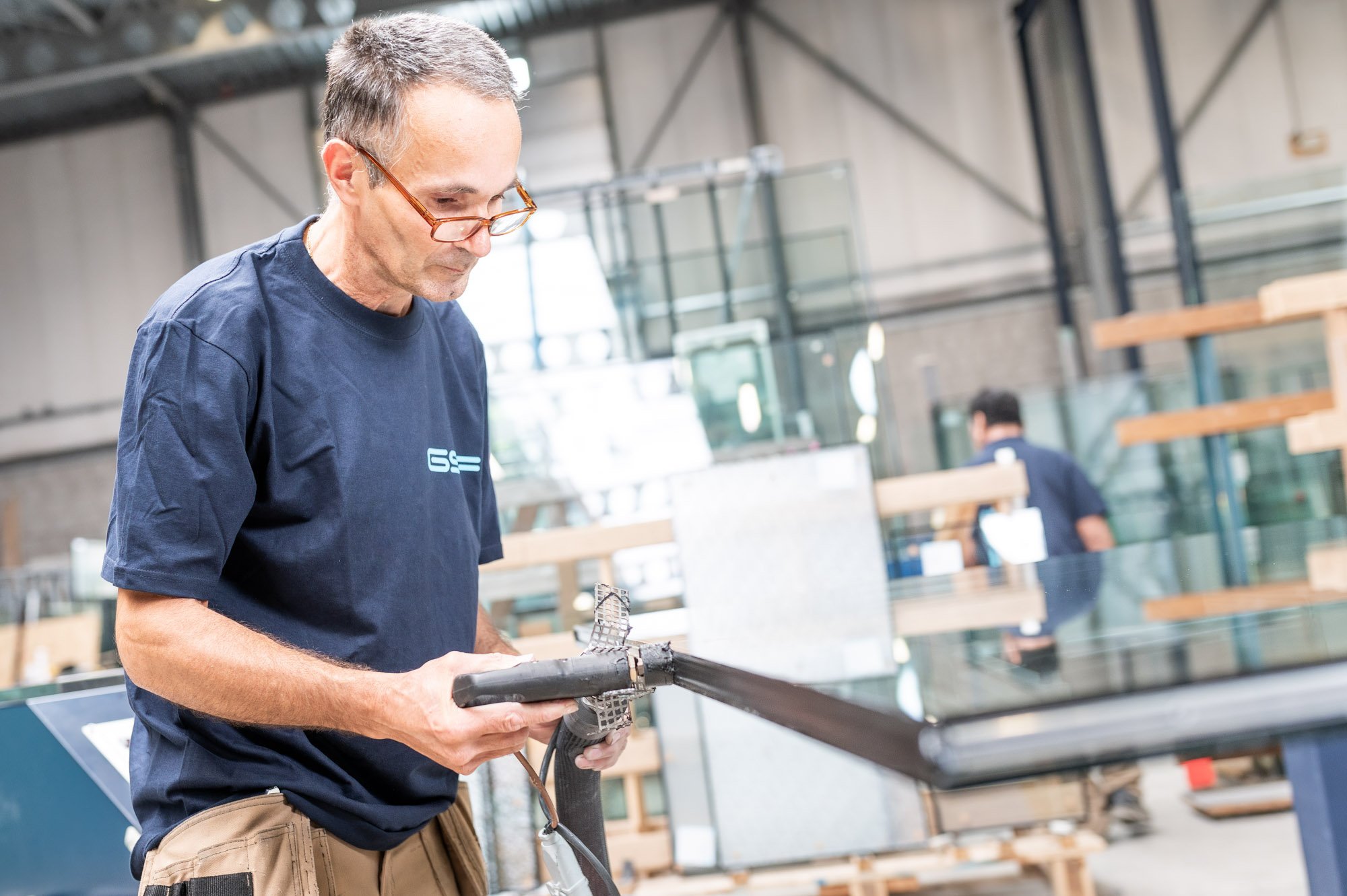
Maatschappelijke en commerciële impact
Het vergde flink wat investeringen om het circulaire isolatieglas – dat GSF Glasgroep verkoopt onder de naam isoMAX - in productie te nemen. Onder andere investeringen in de bokken, de machines en een nieuw pand. Maar het legde het bedrijf geen windeieren. “Sinds we dit doen zijn we extreem gegroeid. We hebben nu 60 medewerkers en komen binnen bij opdrachtgevers waar we anders misschien wel nooit binnen waren gekomen. Dat is iets wat ik hiervan heb geleerd: het heeft zowel commercieel als maatschappelijk gezien heel veel zin om je businessmodel eens kritisch onder de loep te nemen en aan te passen. En met een kleine aanpassing kan je al veel verschil maken.”
“Ik ben ook verrast door het enthousiasme van iedereen. Bij opdrachtgevers, maar ook bij medewerkers. Ik krijg continu mailtjes van mensen die bij ons willen komen werken, omdat ze willen bijdragen aan een mooiere manier van produceren. En de grootste verrassing was misschien wel dat het zo makkelijk ging. Want wat aan het begin zo moeilijk leek, uitzoeken of het zou kunnen, was uiteindelijk heel makkelijk door de grote interesse vanuit universiteiten om het te onderzoeken en opdrachtgevers om het toe te passen.”
72% lagere MKI
Het onderzoek van de Hogeschool van Amsterdam en TU Delft leverde onder andere een levenscyclusanalyse op van circulair isolatieglas. Die was alleen nog wel gebaseerd op aannames. “Toen het begon te lopen moesten we natuurlijk waterdicht bewijs aanleveren. Daarom heeft Alba Concepts voor ons een LCA gemaakt. Daarna is het een kleine moeite om opgenomen te worden in de Nationale Milieudatabase.”
“Nu blijkt dat ons circulaire isolatieglas een flink lagere MKI heeft dan traditioneel isolatieglas. Onze categorie 1-data komen uit op milieukosten van €1,72 bij een levensduur van 30 jaar. Bij traditioneel isolatieglas komt de MKI in de categorie 2-data uit op €4,62. Ik heb af en toe glasproducenten op bezoek die ernaar vragen. Dan is het fijn dat je zulke harde cijfers kan laten zien. Daarover bestaat geen discussie.”
Gelijkwaardige circulaire glasfabriek
Ambities heeft GSF Glasgroep nog genoeg. “Ons circulaire isolatieglas is nu ongeveer 10% duurder dan traditioneel isolatieglas. Dat is niet veel, maar voor nieuwbouwprojecten soms nog wel een drempel. Daarnaast zijn we natuurlijk gebonden aan de oogst die we binnenkrijgen. Jaarlijks wordt er in Nederland 400 ton aan glas gevraagd en komt er 100 ton aan afvalglas vrij. We zijn dus geen eindoplossing voor de totale glasvraag in Nederland, maar kunnen zeker wel in een deel voorzien.”
“Onze ambitie is om een circulaire glasfabriek te ontwikkelen die qua prijs en volume gelijkwaardig is aan een traditionele glasfabriek. We zijn daarmee al een heel eind op weg. We weten ook zeker dat het kan.”
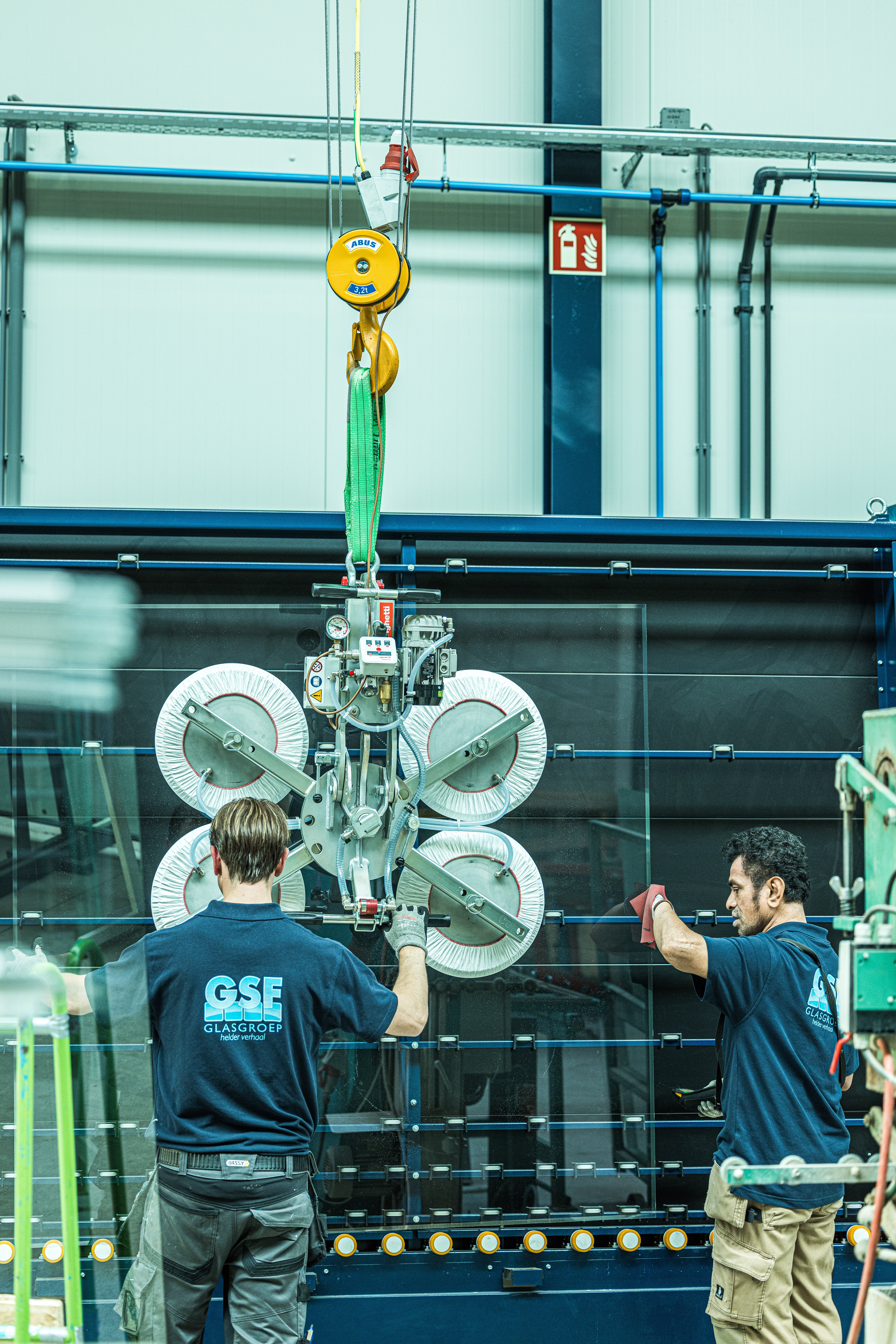
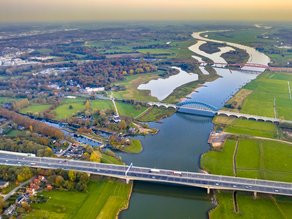
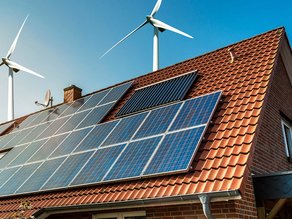
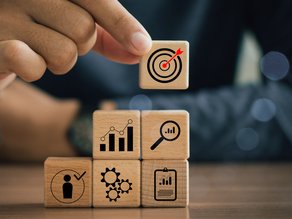
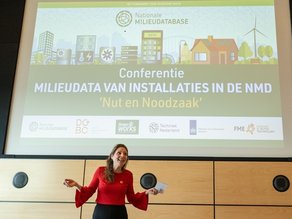